How to treat and prove adhesion on medical devices
Surface treatment plays a crucial role in the medical device industry, particularly when it comes to enhancing adhesion properties and improving surface energy.
Understanding Plasma and Corona Treatment
Plasma treatment and corona treatment are two widely used methods for surface modification, specially used in the medical device industry. These treatments involve modifying the chemical structures on the top layer of plastic parts’ molecules, leading to improved adhesion and coating capabilities.
By breaking the tight molecular bonds of low surface energy materials, plasma and corona treatment create a receptive surface that allows for better bonding, ink adhesion, and coating application.
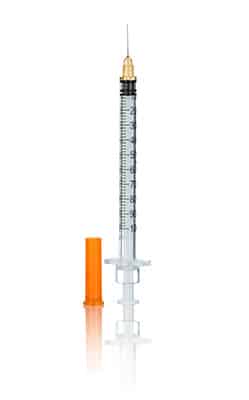
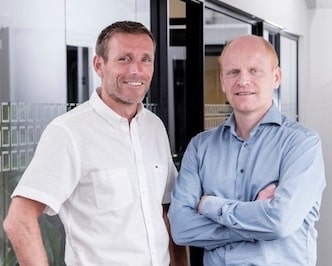
Solving your adhesion problems
We have more than 50 years of experience in delivering and manufacturing quality, high-end surface treatment products for any industry.
Tantec has both standard machines, but also custom-designed machines.
Contact us today and get a quote. We are standing by to service you.
Solving your adhesion problems
We have more than 50 years of experience in delivering and manufacturing quality, high-end surface treatment products for any industry.
Tantec has both standard machines, but also custom-designed machines.
Contact us today and get a quote. We are standing by to service you.
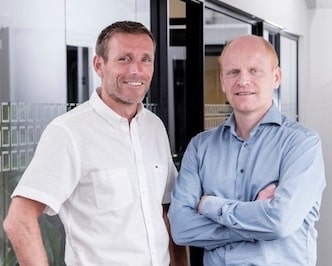
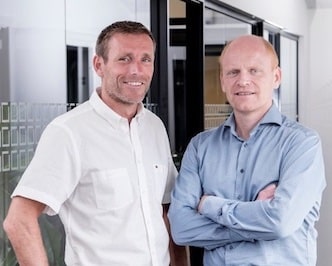
Solving your adhesion problems
We have more than 50 years of experience in delivering and manufacturing quality, high-end surface treatment products for any industry.
Tantec has both standard machines, but also custom-designed machines.
Contact us today and get a quote. We are standing by to service you.
Overcoming Adhesion Challenges in Medical Devices
In the medical device industry, ensuring proper adhesion is crucial for meeting FDA and other regulations and maintaining the integrity of products. Low surface energy materials like polystyrene, polypropylene, and polyethylene pose significant challenges in terms of adhesion and coating.
Plasma and corona treatment offer effective solutions to enhance surface energy, enabling proper adhesion and coating application. These treatments create peaks and valleys on the surface, facilitating ink or coating acceptance and promoting uniform treatment.
Customizable Solutions for Medical Device Surface Treatment
Tantec’s strength lies in providing tailored solutions to address specific challenges in the medical device industry. Our unique rotational corona-based process, known as RotoTEC, offers a uniform treatment across large and tall parts, making it ideal for tissue culture products, ophthalmic lenses, and more.
Additionally, our SyrinTEC system provides comprehensive treatment for syringes, including both the inside and outside surfaces. 360 degrees treatment on parts. We also specialize in treating hard-to-reach areas such as needle hubs, ensuring improved adhesion and glue wettability.
Ensuring Product Quality and Compliance
Surface treatment with plasma and corona technologies is an accepted practice in the medical device industry. Our solutions not only enhance adhesion but also meet FDA and other regulations. Tantec’s systems are designed to provide a precise and uniform treatment, ensuring that the cosmetic and structural integrity of the medical device remains intact. The improved print quality, adhesion, and coating durability contribute to the overall reliability and traceability of the product.
Tantec is a Leader in Corona and Plasma Treatment
Tantec has been a prominent player in the corona and plasma industry for several decades. With a comprehensive range of standard and customized products, Tantec caters to the specific needs of medical device manufacturers worldwide. Our vast network of agents spanning over 30 countries, ensures that we offer effective solutions tailored to individual requirements.
Surface treatment using plasma and corona technologies is a vital aspect of the medical device industry. Tantec, with its expertise and specialized solutions, stands ready to help manufacturers overcome adhesion challenges and meet FDA and other regulations. By leveraging our cutting-edge treatment systems and comprehensive testing capabilities, we ensure that medical devices maintain their structural integrity, while achieving enhanced adhesion, coating, and print quality.

