Plasma Treaters
Surface treatment with Plasma treatment technology offers innovative solutions to adhesion and wetting problems in many industries.
Our plasma treaters can be used to treat many different materials .e.g. like metals, plastics or glass, and they can be used in various settings and industries.
PlasmaTEC-X
PlasmaTEC-X OEM
Tantec’s New PlasmaTEC-X Atmospheric Plasma treatment system is built around the concept of a high voltage DC Plasma discharge…
PlasmaTEC-X UR
Tantec A/S has received Universal Robots (UR) certification for its PlasmaTEC-X surface treatment solution…
ProfileTEC
ProfileTEC: Two common applications for pre-treatment of automotive EPDM profiles with plasma are prior to flocking and slip-coating.
RotoVAC
Tantec RotoVAC vacuum plasma treater is designed for plasma treatment of small injection moulded plastic parts…
SpinTEC
SpinTEC is with AC motor for spinning of 2 pcs. PlasmaTEC-X nozzles pointing inwards for uniform treatment and to minimize heat impact.
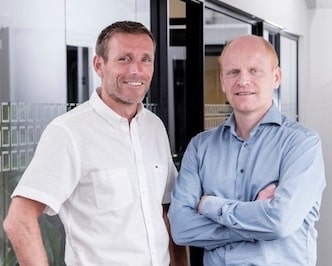
Solving your adhesion problems
We have more than 50 years of experience in delivering and manufacturing quality, high-end surface treatment products for any industry.
Tantec has both standard machines, but also custom-designed machines.
Contact us today and get a quote. We are standing by to service you.
Solving your adhesion problems
We have more than 50 years of experience in delivering and manufacturing quality, high-end surface treatment products for any industry.
Tantec has both standard machines, but also custom-designed machines.
Contact us today and get a quote. We are standing by to service you.
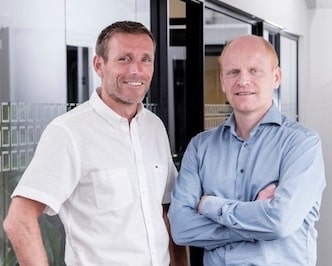
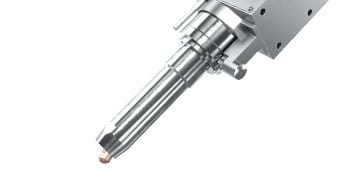
SpinTEC30
SpinTEC30 – The most compact rotary plasma system
VacuTEC
Tantec´s VacuTEC Plasma Treater is designed for plasma treatment of a large number of different injection moulded parts…
VacuTEC 2020
Tantecs VacuTEC-2020 Plasma Treater is designed for treatment of a large number of different injection moulded parts. The VacuTEC offers very fast…
VacuTEC 5050
Tantecs VacuTEC 5050 Plasma Treater is designed for treatment of a large number of different injection moulded parts. The plasma treater offers…
VacuTEC 8080
Tantec’s VacuTEC 8080 Plasma Treater is designed for the treatment of a large number of different injection molded parts.
VacuTEC 100100
Tantecs VacuTEC 100100 Plasma Treater is designed for treatment of a large number of different injection moulded parts. The plasma treater offers…
VacuLine
Standard and customised vacuum plasma treaters. The Tantec VacuLINE plasma treater is designed for treatment of a variety of….
OzoneTEC
Tantec has developed their OzoneTEC System to treat the inside of products such as surfboards, coolers, ice boxes, jacket pipes, small boats etc…
ZeroNOxTEC
ZeroNOxTEC – Plasma Treatment with no NOx emissions

Why use a plasma treater?
Component preparation is an important step prior to bonding, painting, varnishing, and coating processes. Plasma treatment using one of our plasma treaters provides an economical solution for the cleaning and activation of component surfaces before further processing. Plasma surface treatment improves wettability and adhesion of ink, glues, and coatings on many different surfaces.
If you need to understand the technology behind the surface treatment technology, we advise you to take a look at our article about: Surface treatment and how it works.
Our Plasma Treatment equipment and products are cost-effective
Plasma treatment provides surface treatment and an economical solution for the cleaning (plasma etching) and activation of complex surfaces before further processing. This is especially true for profiles with complex surfaces, that cannot be treated using regular corona treatment mechanisms. Our plasma surface treatment equipment is used for long-term adhesive bonding of plastics and metals, and we have many customizable solutions suiting your company and your products.
Plasma treatment is used in almost all industrial manufacturing processes, and we have more than 50 years of experience in delivering the right equipment for surface treating any material.

What are the key features to look for in a plasma cleaning machine?
When selecting a plasma cleaning machine, key features to consider include:
- Surface compatibility: Ensure the machine can handle a variety of materials such as elastomers, metals, plastics, ceramics, and glass.
- Contaminant removal: The machine should effectively remove surface oxidation, mineral oil residues, and organic contaminants.
- Environmentally friendly: Look for machines that eliminate the need for chemical solvents, making the process more environmentally friendly.
- Operational costs: Consider machines with low operational and maintenance costs.
- Surface preparation: The machine should be capable of preparing surfaces for various processes like potting, printing, coating, and painting.
- Ease of use: Opt for operator-friendly machines that are easy to use and maintain.
- Customization: Availability of both standard and custom-designed machines to meet specific industry needs.
These features ensure that the plasma cleaning machine provides high-quality, efficient, and environmentally friendly cleaning solutions.
Can plasma cleaning be customized for specific applications?
Yes, plasma cleaning can be customized for specific applications. Tantec offers both standard machines and custom-designed machines to meet the unique needs of various industries. This customization ensures that the plasma cleaning systems are tailored to effectively clean and prepare surfaces for specific manufacturing processes, such as potting, printing, coating, and painting.
What maintenance is required for plasma cleaning equipment?
Maintenance for plasma cleaning equipment typically includes:
- Regular cleaning: Ensure that the electrodes, chamber, and other components are clean to maintain optimal performance.
- Inspection of components: Regularly check for wear and tear on electrodes, seals, and gas lines.
- Calibration: periodically calibrate the equipment to ensure accurate performance and consistent results.
- Software updates: Keep the system’s software up to date to benefit from the latest features and improvements.
- Gas supply: Monitor and maintain the gas supply to ensure there are no leaks and that the gas is pure and at the correct pressure.

What are the steps involved in setting up a plasma cleaning equipment?
Setting up a plasma cleaning system involves several key steps to ensure optimal performance and effective surface cleaning. Here are the general steps:
- Assessment of requirements: Determine the specific cleaning needs based on the materials and contaminants involved. Decide whether a standard or custom-designed plasma cleaning machine is required.
- Selection of equipment: Choose the appropriate plasma cleaning system from Tantec’s range of products, such as PlasmaTEC-X, VacuTEC, or other suitable models.
- Installation: Install the plasma cleaning machine in the designated area, ensuring it is placed in a clean and controlled environment. Connect the machine to the necessary power supply and gas sources (e.g., oxygen, argon).
- Calibration and testing: Calibrate the machine according to the manufacturer’s guidelines. Perform initial tests to ensure the system is functioning correctly and achieving the desired cleaning results.
- Operator training: Train operators on how to use the plasma cleaning system safely and effectively. Provide instructions on routine maintenance and troubleshooting.
Routine maintenance: Establish a maintenance schedule to keep the machine in optimal working condition. Regularly check and replace consumables, such as gas supplies and filters.
These steps help ensure the plasma cleaning system is set up correctly and operates efficiently for various surface cleaning applications.


