Surface Treatment of metals, using dry etching
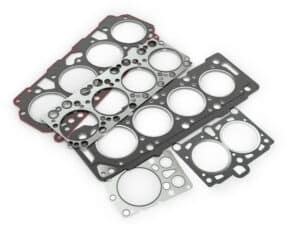
Gaskets for cylinder car engine.
Enhance your metal surfaces with advanced etching metal techniques. Whether you’re working on etching steel for automotive parts or other industrial applications, our cutting-edge methods deliver precision and durability.
The Importance of Metal Etching in Industry
Etching metal surfaces is a critical process across various industries. From etching steel for automotive bodies to treating stainless steel for construction materials, this ancient technique, dating back to 4000 BC, remains essential in modern manufacturing.
Why use surface treament of metals?
Today there can be several reasons why it is necessary to change the surface properties of metals. For example is surface treatment of metals used for:
- Decoration and/or reflectivity
- Improved hardness (eg. for resistance to damage and wear)
- Prevention of corrosion
Surface treatment of metal surfaces plays an enormous role in extending the life of metals, such as in automotive bodies and construction materials, an often seen application is cleaning of stainless steel bodies for windows, etc. To achive these benefits, you can dry etch metals, using plasma surface treatment.
Etching steel and etching metals (video)
Understand what happens when you etch metal or glass in this short video explainer.
What industries use metal surface treatment?
Almost every industry will have a need for metal etching surface treatment equipment.
Among the industries who today use metal surface treatment include the following; the automotive industry, the construction industry, the container industry, the electrical industry, the medical industry, industrial equipment, industries using laboratory equipment, aerospace, and several other industries.
The range of components treated varies from: spectacle frames, components for automotive, screws, nuts, bolts, different tools and many other.
How does Tantec treat metal surfaces?
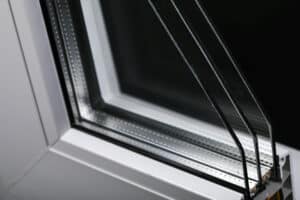
Plastic window profile with triple glazing.
Metal surfaces can be treated by using special insulated electrodes or the PlasmaTEC-X surface treatment nozzles.
Treatment or etching of metal surfaces is often a matter of both cleaning and surface activation. Often Stainless steel surfaces are treated with either Ceramic Corona Electrodes or PlasmaTEC nozzles to ensure max. wettability and plasma cleaning before bonding.
Tantec produces several solutions for metal surface treatment. You may view our list of surface treatment products: Plasma treaters and Corona treaters.
Should you have further questions, do not hesitate, our specialists are here to help.
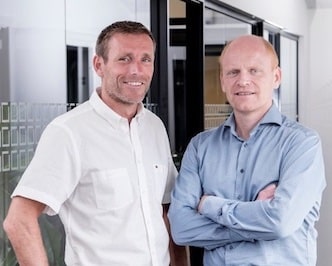
Solving your adhesion problems
We have more than 50 years of experience in delivering and manufacturing quality, high-end surface treatment products for any industry.
Tantec has both standard machines, but also custom-designed machines.
Contact us today and get a quote. We are standing by to service you.
Expert Solutions for Metal Etching
At Tantec, we specialize in 3D etching of metal surfaces with even, uniform treatment. Our in-house testing facilities ensure that we provide the best possible solutions for your etching steel and etching metal needs.
The coating process using plasma
Treating metal surfaces is primarily, as mentioned above, a surface cleaning issue. Here Plasma treatment often proves to be the best solution when a metal surface needs treatment.
Plasma treatment is a process designed to change the surface properties of a substrate to increase surface energy and/or make it chemically compatibility with a bonding material.
Surface treatment creates an electron bombardment that breaks the surfaces chemical bonds while the ions hitting the surface are designed to alter the chemical composition of the surface.
Plasma systems may also be used to treat a variety of material types including polymers, glass and ceramics.
Understanding the Surface Treatment of Metal
Compared to other surfaces that need treatment prior to coating, printing, or adhesion etc. there are a number of different methods available for the surface treatment of metal. The treatment of metal is a process in which parts or components made out of metal are treated before any actual coating takes place.
The purpose of this etching treatment is increasing the surface energy level of a particular metal surface so that it can easily adhere to the printing or coating that is about take place. This type of treatment is usually known as the coatings pretreatment. Treatment of metal involves the creation of a barrier that acts like a wall protecting the metal in an environment that’s corrosive.
The surface layer forming on a metal that is scheduled for chemical coating is created due to a chemical reaction that’s non-electrolytic in nature. The reaction occurs between a solution and the metals surface. These layers are amorphous and adherent. For allowing the treatment of metal to form a shielding layer, the metal being used as a base should be converted into a component that’s less reactive towards corrosion in comparison to the metal surface being used in the first place.
In order to conduct a successful surface treatment of metal, the layer formed on the metals surface should be able to pass on the same amount of potential throughout. The layer should also be able to neutralize any areas showing signs of cathodic or anodic corrosion. Only then can surface treatment of metal provide a base that’s absorptive for adhesion to paints and other finishes.
The process of metal surface treatment involves more than a few steps. Firstly, the stamping compounds and mill oils are cleaned away from the surface leading to rinsing post phosphates. This is followed by the application of an organic-inorganic sealer. And finally, the surface is rinsed with water that’s free of contaminants e.g. water obtained through reverse osmosis or deionization. After being rinsed, the surface is taken to an oven that dries off the surface. Here, all the moisture is completely removed before a metal can enter the painting process.
Types of Conversion Coatings
There are several types of conversion coatings used in the surface treatment process. Some of these are given below.
Coating with Oxides
Coatings done by the help of oxides are actually corrosion products that include an oxide with negligible thickness leading to good adhesion. These treatments are usually done through electrochemical reactions, heat, or chemicals.
Chromate Coating
These coatings involve the process of chemical conversion formed by a reaction occurring between chromium salts or chromic acid water solutions. Chromate coatings can be applied on cadmium, zinc, magnesium and aluminum because of their resistance towards atmospheric corrosion. These coatings are extensively used for protecting hardware items used as household products.
Phosphate Coating
These coatings also involve chemical conversion of metal surfaces. Phosphate crystals are formed on material surfaces containing zinc, manganese or iron phosphates. Generally, phosphate coatings are applied on cast iron, low-alloy steel and carbon steel. Though, these can be applied on cadmium, tin, aluminum and zinc too.
Surface treatment illustrated in video
Watch this video to see how suface treatment works.
Which materials can be successfully treated?
Almost all commonly used base materials are easily treated. The material list below includes materials both plastic and metals:
PP | PE | PES | Teflon (PTFE) |
Cross Linked Polymers | PC | ABS | PS |
EPDM | TPF | TPE | Stainless Steel |
Aluminium | Many other metals |
If you want to know, if your metal surface would benefit from a corona/plasma treatment, then send your sample for a test free of charge in our testing facilities!
At Tantec we are experienced in developing solutions to the automotive industry and our core competences is 3D treatment with even and uniform treatment with durable effect. We have our own in-house testing facilities and offer a free test of your part. Send a sample and explain your project to us. After testing, you will receive a documented report and we advise you in the best suitable treatment solution.
Europe/International – Send your sample to: – Tantec A/S – Industrivej 6 – 6640 Lunderskov – Denmark
United States of America – Send your sample to: – Tantec EST Inc. – 160 North Brandon Drive – Glendale Heights – IL 60139 – U.S.A.

Video: VacuTEC | Vacuum Plasma Treater

