Leak detection of micro pinholes | LeakTEC
Leak Detection Process
LeakTEC is a powerful electronic tool for non-destructive leak detection of non-conductive single layer materials.
The LeakTEC measures a leak between a high-voltage electrode (DC) and counter electrode which can either be grounded or running opposed polarity. The LeakTEC ensures full process control and traceability.
Test to detect pin holes
It is typical in field applications to surface test moulded and welded joints in medical devices like medical tubes, containers, pipettes, cannulas and extruded film for medical bags etc.
This fully automatic test is capable of detecting pin holes even smaller than 3 microns by introducing an electrical potential between a detecting electrode and an electrical ground, (i.e. metal jig or mandrel holding the part) while the plastic part itself acts as the insulator.
How the detection works
In the event of detecting a crack or pin hole in the plastic material, an electrical contact is established between electrode and ground.
This pass/fail contact is processed via the integral generator module interfaced with the main machine control.
The machine control can either enable a downstream ‘part-reject’ function or track trends in the manufacturing process, which can be fed back for early process adjustment or maintenance.
Counter Electrode Measurement and Function
Counter electrodes measurement is to ensure that all electrodes are fully working. Each counter electrode will then give out individual signal to be processed by the machine PLC unit.
To limit the high-voltage and minimize generation of static electricity Tantec offers its dual polarity system (patented).
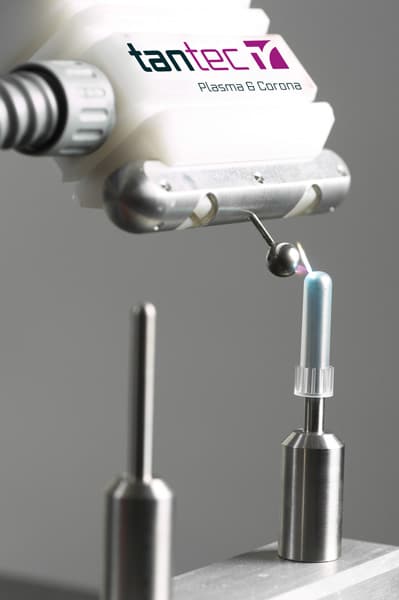

Leak Detection Technology
Tantec’s leak detection technology has its roots in the company’s Corona technology, which is capable of detecting arcs when a high voltage probe finds a path to ground.
This technology has been adapted to create a leak detection process, offering non-destructive testing of plastic injection molded parts. This process helps determine if a hole is present in the part without damaging it, making it an invaluable tool in manufacturing industries.
Did you know our leak detection system can detect pin holes even smaller than 3 microns. 3 microns is 0.003 millimeters!
How it Works
Tantec’s leak detection process works only on non-conductive materials like injection molded parts. The parts should have an opening on the bottom and a closed end on the other side or a flat wall or sheet that isolates ground from high voltage, allowing for the detection process.
The process uses a DC voltage to measure the voltage or the detection between the plastic and the high voltage, and only creates by products or electrical discharge when a leak is present. When a detection is present, there will be an arc that passes through to the metal, and the generator will provide a signal indicating the detection or failure mode.
The setup includes a generator, a transformer, a high voltage cable, a grounded base, and a high voltage probe when showing how the system works. A good part passes if no failure mode is detected, while a bad part has an alarm condition that pops up in the right-hand screen corner, indicating that a path to ground has been found.
The Importance of DC Voltage in Leak Detection
Leak detection is a critical process in various industries, and the choice of voltage plays a crucial role. Tantec’s systems utilize DC voltage, typically in the 10 to 17,000 Volt range, to avoid the creation of Corona during the detection process. This ensures a clear pass or fail outcome, allowing for accurate and quick identification of defects.
What defines a DC Voltage?
DC Voltage, or Direct Current Voltage, is a unidirectional flow of electric charge. Unlike AC Voltage (Alternating Current), DC Voltage remains constant over time and is used in Tantec’s leak detection to avoid creating Corona, making it ideal to identify materials with or without holes.
Describe the automatic leak detection (small video)
Video description: The automatic leak detection process involves applying high DC voltage to the part under test. The grounded fixture, known as the counter electrode, helps in detecting a path to the ground if there is a hole. An arc signal is generated to the PLC if a hole is found, giving instant feedback.
What is good using the DC Process Voltage?
Using DC Voltage ensures precision, avoids false failures, and enables clear distinction between pass and fail conditions, improving the reliability of the process.
When and why does it provide a signal?
A signal is provided when a hole is detected, allowing the current to find its path to the ground. This signals a failure mode, indicating that the part should be rejected.
How does it provide a signal?
The signal is provided through an arc alarm generated to the PLC, and feedback is given on the screen.
Opposed Polarity Detection Process
Tantec’s opposed polarity detection process provides two values or additions beyond its Leak Detection. It reduces some of the static present during the detection process and allows for higher voltage to detect even smaller holes. The higher the voltage, the smaller the hole that can be found, allowing for the passage of the dielectric layer or opening and getting the high voltage to find its way to the ground. This process increases the accuracy of leak detection, ensuring product integrity and reducing the risk of wastage.
Application in Injection Molding
Leak detection technology is particularly useful in the injection molding industry. Tantec’s leak detection systems can be designed and developed to fit specific applications, ensuring a tailored solution for each manufacturer. These systems can test individual parts or multiple parts simultaneously, allowing manufacturers to identify defective parts quickly and efficiently.
Tantec’s leak detection technology can detect holes down to the micron range, ensuring a high level of accuracy in identifying leaks. Manufacturers can send samples for testing and verification, allowing them to evaluate the effectiveness of the technology for their specific needs.
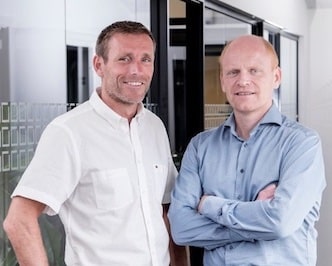
Solving your adhesion problems
We have more than 50 years of experience in delivering and manufacturing quality, high-end surface treatment products for any industry.
Tantec has both standard machines, but also custom-designed machines.
Contact us today and get a quote. We are standing by to service you.
System Design and Development
Tantec’s systems are designed and developed to fit the application of its customers. It can provide both the holder for the part and the high voltage probe or just the high voltage probe if the part is already sitting on an existing mandrel or fixture that is usable by Tantec.
They are tailored to meet your specific requirements, offering flexibility to test individual holes or particular areas, ensuring optimal quality control.
Individual Detections and Trends
Tantec’s system can do individual detections, enabling its customers to test all their parts at once and know which ones have failed. This feature helps in finding trends in the injection molding process, indicating problems with the mold and allowing adjustments to eliminate downtime as much as possible.
Sample Testing
We at Tantec recommend that you send samples to test its fixtures and see if we can detect the holes. Tantec can provide feedback on the holes found or not found, making it an excellent way to help prove out the concept and value of the system.
Case Studies
Tantec has worked with several injection molding companies over the years, and these companies have been happy with the process and control provided. The leak detection technology helps in building and developing their business by ensuring the product integrity they are shipping out to their customers.
Case example 1:
A long-standing customer in the injection molding industry has been using Tantec’s leak detection technology for many years. They have integrated the technology into their manufacturing process, running 24/7 with minimal operator intervention. The leak detection system has provided them with a high level of quality control, ensuring product integrity and reducing wastage.
Case example 2:
This case involves a company that uses Tantec’s leak detection technology to test 48 to 64 tubes at a time, taken directly from the injection molding machine. This high-throughput system allows for efficient testing and helps maintain product integrity throughout the manufacturing process.
Leak detection technology benefits
Tantec’s leak detection technology is a great non-destructive testing, providing accurate and efficient leak detection solutions for injection molded parts. With the ability to detect even the smallest holes, Tantec’s technology ensures product integrity and reduces wastage. The technology does no damage on the part, reduces downtime and ensures product integrity. Manufacturers looking to improve their quality control processes should consider integrating Tantec’s leak detection technology into their operations.
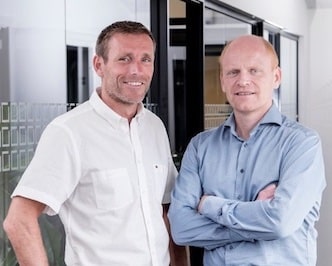
Solving your adhesion problems
We have more than 50 years of experience in delivering and manufacturing quality, high-end surface treatment products for any industry.
Tantec has both standard machines, but also custom-designed machines.
Contact us today and get a quote. We are standing by to service you.
What can Tantec do for you if you are interested?
Tantec offers a state-of-the-art leak detection system designed to identify holes in plastic parts. With full application labs in Chicago and Denmark, Tantec provides personalized services like sample testing, mock-up fixture designing, and continuous support to ensure the success of your manufacturing process.
Limitations and Considerations
While Tantec’s leak detection system offers precision, some limitations exist, such as the inability to test closed bags or multi-layer parts. However, the system is versatile enough to detect leaks on a larger area of the part, not just specific spots, with certain restrictions. The positioning of the high voltage probe also plays a significant role, with an ideal distance of about one millimeter from the part.
Tantec’s Support and Future Webinars
Tantec provides robust support, including an applications lab in Chicago and Denmark, to assist with sample testing and process development. Moreover, the company hosts webinars to educate and engage with customers, offering a platform for questions, insights, and demonstrations.
Tantec’s leak detection systems represent a combination of technological innovation and practical application. By employing DC voltage, providing real-time feedback, and understanding the limitations of the process, Tantec ensures quality control in manufacturing. The demonstrations, webinars, and availability of the applications lab further enhance the customer’s experience and confidence in the Tantec brand. Future engagements and continued development, promise to keep Tantec at the forefront of leak detection technology.
Tantec’s Leak Detection System is an advanced solution for manufacturers seeking reliability and precision in identifying leaks. With its quick, accurate, and customized approach, Tantec ensures quality and supports your unique manufacturing needs.
Leak detection FAQ
Why use leak detection?
To easily determine if a hole is present without damaging the part. It ensures product integrity, reduces the risk of leakage, and helps identify potential issues in the injection molding process.
Value of the process
The leak detection process provides valuable insights into product quality and injection molding processes. It helps identify trends, reduce waste, maintain product integrity, and ensure customer satisfaction. Additionally, it can be integrated with automation systems for minimal operator intervention.
Parts able to be leak detected?
Leak detection works best on non-conductive materials, such as injection molded parts with an opening on one end and a closed end on the other, or flat walls or sheets. It’s crucial to have an open end for grounding and high voltage on the opposite side, to create an electrical field for the detection process.
Detection process time
The detection process time is typically between half a second to one second. Going longer than this is usually not necessary, as fine-tuning adjustments in terms of voltage can be made instead.
What is the smallest hole to detect?
The smallest hole detection capability depends on the exact setup and requirements of your manufacturing process.
How far down to detect?
Tantec’s system can detect along the length of a part, including tubes, though there may be limitations near the open end.
Can you detect a hole in a multi-layer part like a closed bag?
No, detecting holes in closed bags or multi-layer parts is not possible with this technology as it requires access to both sides of the film.
Can you detect leaks on a large area on a part?
Yes, Tantec’s system can detect leaks on larger areas of a part, though some limitations may exist near the open end.
What is the typical distance that you want your high Voltage to be, to test parts during the process?
The high voltage probe should ideally be about one millimeter or closer to the part, while the grounded side should be as close as possible to ensure precision.
Is there any gas generated by the arc when the hole is detected?
No, the DC Arc does not generate any gas. It does create a large arc that expands the hole but produces no byproducts.
How long is the typical detection process time?
The typical detection process time is about half a second to one second.
Why is the detection process time not longer?
The process is designed for efficiency and accuracy, allowing quick detection without compromising the quality of the inspection.

Technical specifications
FEATURES: | |
Easy to install and use | Uncomplicated operation into the production line. |
Fast detection times | Pin hole detection is done either in-line or during stop at index movement. Typical test times from 0.03 seconds. |
Dual polarity detection (patented) | Limits high-voltage and minimizes generation of static electricity. |
Full integration | Must be fully integrated into existing production lines. |
High precision test electrodes | For testing small fragile parts. |
Non-destructive testing | Tested parts remain undamaged allowing for zero waste. |
Single or multiple part detection | Adding counter electrode measurement allows for testing of multiple parts. |
No corona discharge | Use of DC voltage eliminates corona discharge. |
Technical Specifications | LeakTEC Plasma Treater |
Mains voltage and frequency | 230 VAC 50/60 Hz |
Output voltage/test power | Max. 40 kv/max. 2000 Watt |
Power supply | HV-X plasma generator series |
Detection times | From 0.03 sec. (other on request) |
Number parts per batch | Customised |
Electrode design | Cusomised to application |
Treatable materials | Non-conductive only |
Part thickness | From 0.1-5.0 mm others on request |
Control and connectivity | Complete with touch panel (Standard-Proface) |
Regulation compliance | CE – RoHs – WEEE |
