Vacuum treating chamber | VacuTEC
Designed for different parts
Tantec’s VacuTEC Plasma Treater is designed for plasma treatment of a large number of different injection molded parts.
The VacuTEC is available with both single and multiple tray configuration.
Fast treatment and optimum adhesion
The VacuTEC offers very fast treatment times and optimum adhesion properties for downstream coating, gluing, painting, and printing applications.
Vacuum treating chamber
In the vacuum treating chamber, a vacuum is built up to between 2 and 12 mbar before an electrical discharge is created through the integrated plasma electrode. Treatment cycle times are often short, between 2-120 seconds depending on the material and its formulation.
An appriciated machine
The VacuTEC is appreciated for its simplicity of operation, reliability in production, and fast process speed. Treating gasses such as argon and oxygen can be applied, but in most cases, this is not necessary due to the high power exposed by the plasma discharge.
VacuTEC uses the advanced Tantec power generator HV-X series as a power supply and specially designed plasma transformers to provide voltage to the plasma electrodes.
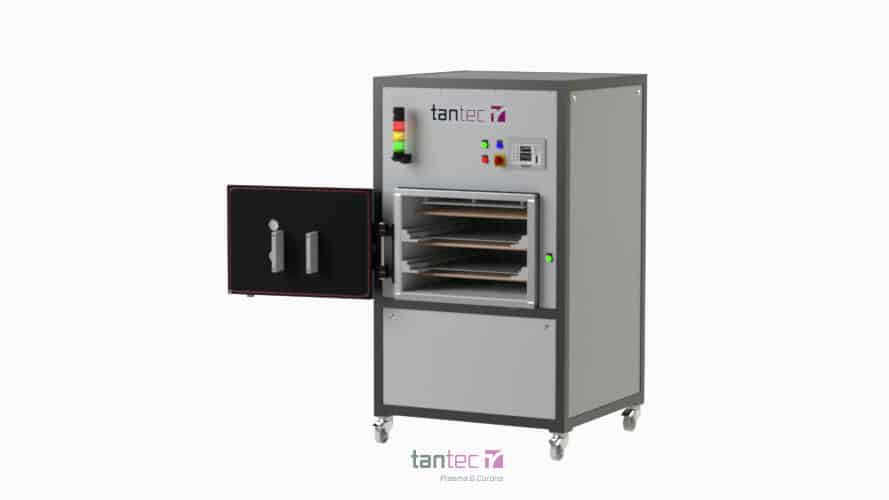
Revolutionizing Surface Treatment for Various Industries
Vacuum plasma technology is a cutting-edge surface treatment process that has been revolutionizing industries like automotive, electronics and medical. This advanced technology offers an efficient and reliable solution for enhancing the adhesion and wettability of various materials such as polypropylene, polyethylene, and ABS. With a focus on ease of use, speed, and flexibility, vacuum plasma treatment systems provide incredible value for businesses looking to optimize their manufacturing processes.
Vacuum Plasma Technology
Vacuum plasma treatment systems are designed to offer a fast and efficient method for improving the adhesion and wettability properties of different materials. Based on the material used, these systems can evacuate chambers in as little as 20-21 seconds, with a 30-second treatment time and a 10-second repressurization time. This speed allows for higher volume production, even with batch processes.
Safety features and monitoring capabilities are built into the system, ensuring that the process is both safe and effective. Vacuum plasma technology provides a uniform treatment on three-dimensional parts without the need for rotation or adjustment during the process. This results in reduced cycle times and increased productivity.
Benefits
It provides the users the ability to adjust various parameters, such as time, pressure, and power, to achieve the desired results. As the technology doesn’t require any special treating gases, it can function with clean, dry air or a combination of oxygen and argon for specific chemical changes.
Customization and Applications
Vacuum plasma treatment systems can be customized according to the needs and specifications of the user. They can be tailored to accommodate different numbers of trays, electrodes, or automation systems, making them suitable for a variety of industries and applications.
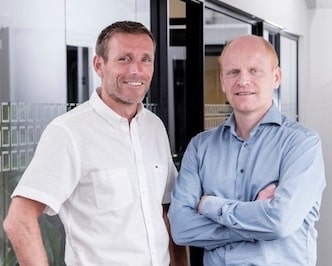
Solving your adhesion problems
We have more than 50 years of experience in delivering and manufacturing quality, high-end surface treatment products for any industry.
Tantec has both standard machines, but also custom-designed machines.
Contact us today and get a quote. We are standing by to service you.
Solving your adhesion problems
We have more than 50 years of experience in delivering and manufacturing quality, high-end surface treatment products for any industry.
Tantec has both standard machines, but also custom-designed machines.
Contact us today and get a quote. We are standing by to service you.
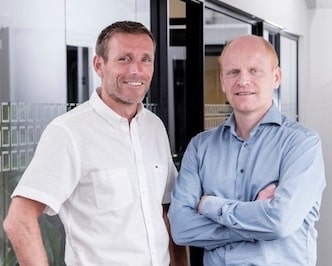
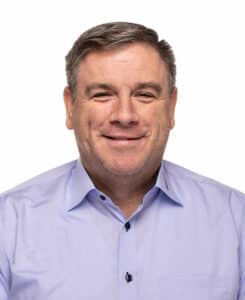
Contact us today and get a quote
We have more than 50 years of experience in delivering and manufacturing quality, high-end surface treatment products for any industry.
Tantec has both standard machines, but also custom-designed machines.
Contact us today and get a quote. We are standing by to service you.
Operation and Factors to Consider
Operating a vacuum plasma treatment system is straightforward. Users can set the process time, pressure, and wattage according to their requirements.
The treatment’s longevity depends on the material being treated and the specific application. For some materials, the treatment can last for several months, while others may only last for a few days to a few weeks. To ensure the best results, it’s recommended to process the parts as quickly as possible after the treatment.
Reliable surface treatment solution
Vacuum plasma technology has significantly impacted various industries by providing a fast, efficient, and reliable surface treatment solution. With its ease of use, speed, and flexibility, this technology offers substantial value for businesses looking to improve their manufacturing processes and the quality of their products.
As vacuum plasma technology continues to evolve, its applications and benefits will only increase, making it an essential tool for industries requiring high-quality surface treatment solutions.
Customized Vacuum Plasma Solutions by Tantec
At Tantec, we understand that every business has unique requirements, and our goal is to provide customized plasma units that seamlessly integrate into your existing workflow, rather than asking you to change your process to fit our equipment.
Designed to Meet Your Needs
We design and develop plasma units that cater to various industries, applications, and materials, ensuring that you receive a tailored solution that matches your production environment. Our systems can be adapted to accommodate different numbers of trays, electrodes, or automation systems, making them suitable for a wide range of applications.
Seamless Integration with Robotics
Furthermore, our plasma units can be designed to be compatible with end-of-arm tooling for robots, enabling easy loading and unloading of trays into the chamber without operator intervention.
This customization provides you with the flexibility and efficiency needed to enhance your manufacturing process, while also allowing for future scaling and growth.
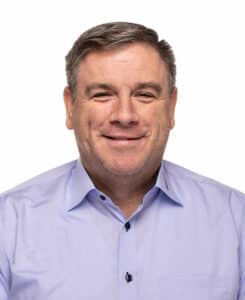
Contact us today and get a quote
We have more than 50 years of experience in delivering and manufacturing quality, high-end surface treatment products for any industry.
Tantec has both standard machines, but also custom-designed machines.
Contact us today and get a quote. We are standing by to service you.
The Benefits of Vacuum Plasma Technology by Tantec
Improved adhesion and wettability: Vacuum plasma treatment effectively increases the surface energy of materials, leading to better adhesion and wettability properties.
- Versatility: Our vacuum plasma systems can handle a wide range of materials, including polypropylene, polyethylene, ABS, and more
- Time efficiency: Our innovative electrode-to-electrode discharge technology allows for fast treatment times, enabling higher volume production with a batch process
- Environmental friendliness: Tantec’s vacuum plasma systems typically use clean, dry air for the process gas, eliminating the need for special treatment gases and reducing environmental impact
What Sets Tantec Apart from Others
Customization: Tantec designs plasma units to fit your needs and process, offering tailored solutions that seamlessly integrate into your workflow.
Expertise: With over 45 years of experience in manufacturing vacuum plasma systems, we possess the knowledge and skills to develop the perfect solution for your application.
Customer-focused approach: We prioritize providing excellent customer service, offering ongoing support and ensuring that our clients receive the best possible results from our vacuum plasma units.
Free Sample Evaluation: How It Works
At Tantec, we offer free sample evaluations to help you determine if our vacuum plasma treatment is the right solution for your application. Here’s how the process works:
- Send us your samples: Ship us the materials or parts you would like to test for compatibility with our vacuum plasma treatment
- Testing: Our team of experts will perform the vacuum plasma treatment on your samples using our equipment in our office
- Reporting: We will provide you with a detailed test report, including before-and-after results, as well as information on pressure, voltage, wattage, and time in the chamber
- Evaluation: You can then evaluate the results to determine if the vacuum plasma treatment meets your requirements and provides the desired value
By offering free sample evaluations, we aim to help you make an informed decision and ensure that our vacuum plasma technology is the best fit for your needs.
Cases

Technical specifications
FEATURES: | |
Easy to install and use | Connects to mains power and compressed air. |
Fast treatment times | High power impact enables treatment times from 20-180 seconds, depending on the material. |
Standard or customized chambers | Chamber and part trays can be designed for most applications. Many available as standard. |
Vacuum level | The plasma discharge is active from 1-12 mbar depending on the application. |
Process gas | Process gasses such as oxygen and argon can be used, but in most cases, it is not necessary. |
Process control | The entire plasma process is controlled by the HV-X generator and the PLC unit. All parameters are displayed through the touch panel. (Standard – Proface). |
Cost-efficient surface treatment | Due to the low power consumption and no need for special treatment gasses, the unit is a very cost-efficient solution for improving surface wettability and adhesion. |
Vacuum pressure Plasma | Enables treatment of both conductive and non-conductive surfaces. |
Chamber doors | Standard doors with a manual opening or automatic motor-driven doors available. |
Technical Specifications | VacuTEC Vacuum Plasma Treater |
Mains voltage and frequency | 100-480 VAC 50/60 Hz |
Output voltage/plasma power | Max. 400 Vp/max. 2000 Watt |
Power supply | HV-X plasma generator series |
Compressed air inlet | 5–6 bar dry & clean |
Process gas | Standard: air, oxygen, argon, nitrogen on request |
Vacuum pump capacity in m³/min. | 15 to 240 m³/min., depending on the size of the vacuum chamber, others on request |
Vacuum level | 1–12 mbar |
Evacuation time, typical | 15-60 seconds, depending on chamber size and pump capacity |
Plasma treatment time, typical | 20–180 seconds, depending on the material |
Control and connectivity | Complete with touch panel. (Standard – Proface) |
Regulation compliance | CE – RoHS – WEEE |