Plasma Bonding: The Cleaning Power of Plasma
Plasma bonding, also known as plasma activation or plasma surface treatment, is a process used to modify the surface properties of a substrate to encourage adhesion. This technique is particularly important in industries where materials that are naturally resistant to bonding need to be joined together. Here’s a deeper look into the process, its applications, and benefits.
Process of plasma bonding
Plasma bonding involves the use of plasma (an ionized gas) to treat the surfaces that are to be bonded. The plasma is generated by applying a strong electric field to a gas (like argon, nitrogen, oxygen, etc.), causing it to ionize. This plasma contains various charged particles, including ions, electrons, and radicals, which interact with the surface of the substrate.
Cleaning
In the plasma bonding process, one of the most critical initial steps is cleaning. The presence of contaminants on a substrate’s surface can severely hinder the effectiveness of bonding. These contaminants can range from natural oils to residues from previous processing steps or environmental dust and debris. Plasma bonding excels in this aspect due to the charged particles’ ability to meticulously clean surfaces at a microscopic level.
During plasma cleaning, the high-energy ions and electrons in the plasma phase interact vigorously with these contaminants, effectively breaking them down or volatilizing them. This plasma-generated cleaning phenomenon ensures that the substrate is free of any materials that could negatively impact the adhesion during the bonding process. As a result, the subsequent bonding steps are conducted on a purely clean surface, which is integral for the strength and durability of the final bond.
Activation
Following the cleaning phase, plasma bonding facilitates the activation of the substrate surface. This stage is crucial as it prepares the surface for successful bonding by increasing its surface energy. The plasma used in plasma bonding contains various active species, including radicals, which are highly effective in modifying the surface at a molecular level.
During plasma activation, these radicals react with the material’s surface, forming new functional groups. These groups are chemically reactive and can form strong chemical bonds with adhesives, coatings, or other substrates. This aspect is particularly significant for materials known for their low surface energy and consequent poor adhesion properties. By creating a chemically reactive surface, plasma bonding sets the stage for a bond that is not only strong but also enduring.
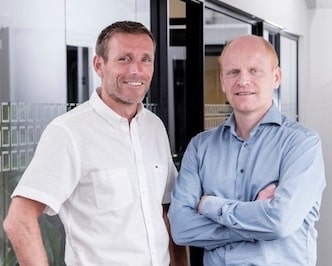
Solving your adhesion problems
We have more than 50 years of experience in delivering and manufacturing quality, high-end surface treatment products for any industry.
Tantec has both standard machines, but also custom-designed machines.
Contact us today and get a quote. We are standing by to service you.
Solving your adhesion problems
We have more than 50 years of experience in delivering and manufacturing quality, high-end surface treatment products for any industry.
Tantec has both standard machines, but also custom-designed machines.
Contact us today and get a quote. We are standing by to service you.
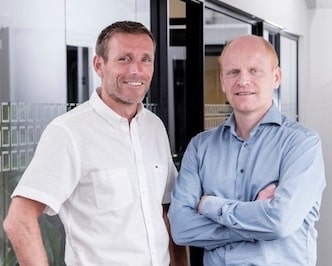
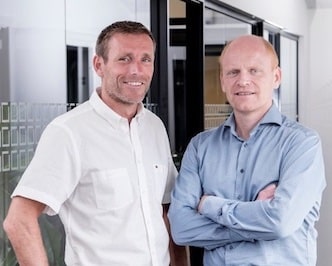
Solving your adhesion problems
We have more than 50 years of experience in delivering and manufacturing quality, high-end surface treatment products for any industry.
Tantec has both standard machines, but also custom-designed machines.
Contact us today and get a quote. We are standing by to service you.
Plasma bonding applications in diverse industries
The versatility of plasma bonding is showcased through its wide range of applications across different sectors. The ability of plasma bonding to modify surfaces at a molecular level makes it indispensable in industries requiring precision and durability. Read on and see how this technique is used in different industries.
Plasma bonding in medical devices
In the medical sector, plasma bonding is a game-changer. Medical devices often comprise materials that are inherently resistant to forming strong bonds. It ensures the secure attachment of various components, crucial for devices that are used in critical medical procedures. The reliability provided by plasma bonding is paramount, considering the stringent standards and hygiene requirements in the medical field. By altering the surface properties at a microscopic level, plasma bonding achieves superior adhesion, contributing to the safety and effectiveness of medical devices
Electronics manufacturing with plasma bonding
The electronics industry continually seeks methods to maintain the integrity of components, especially when miniaturization often results in complex and delicate parts. Plasma bonding comes into play as an invaluable tool for creating robust bonds at microscopic levels. Whether bonding minute components together or ensuring an adhesive meets specific conductivity requirements, this technique provides a solution. It’s especially crucial when traditional adhesives and methods fail to meet the unique demands of electronic product manufacturing, offering durability without compromising on the delicate nature of electronic components.
Automotive innovations through plasma bonding
Durability, resistance to extreme conditions, and longevity are non-negotiables in the automotive industry. Plasma bonding addresses these needs effectively. Various vehicle parts, from internal components to external trim and assembly, can be plasma bonded to ensure resistance against heat, chemicals, and environmental stressors. Plasma bonding’s ability to enhance adhesion between different materials contributes to the vehicles’ overall structural integrity and durability, driving innovation and efficiency in automotive manufacturing processes.
Enhancing packaging with plasma bonding
In the packaging industry, security and durability are just as important as aesthetics. Surface treatment serves a critical role here, especially with plastic packaging. Whether creating airtight seals for food products or ensuring labels and decorative elements adhere strongly and last as long as needed, plasma bonding is the go-to technology. By improving the bond between different materials and surfaces, surface treatment ensures that packaging is not just visually appealing, but also functional and durable, catering to the practical needs of products during transport and storage.
The compelling benefits of plasma bonding
This revolutionary technique in surface engineering, brings forth a multitude of benefits that transcend various industrial needs. Its impact is not just surface-level; it’s a process that enhances product quality, durability, and even environmental sustainability. Here’s how plasma bonding is making a significant difference:
Versatility in materials with plasma bonding
One of the standout advantages is its remarkable versatility. Different industries often work with a diverse array of materials, from common plastics to metals and glass. Plasma bonding rises to the challenge by providing a universal solution for surface treatment across these materials. The process doesn’t discriminate; whether you’re working with a malleable material like plastic or a robust one like metal. This technique modifies the surface to ensure an optimal level of adhesion is achieved.
Durability ensured by plasma bonding
When it comes to creating bonds that last, plasma treatment holds a superior position. Traditional bonding methods often fall short in longevity, struggling to withstand environmental stressors or the wear and tear of regular use. Plasma bonding, on the other hand, creates bonds renowned for their strength and durability. The process fundamentally alters the surface, enhancing its chemical compatibility with adhesives or other substrates. This results in a bond that can endure stress, pressure, and time, making plasma bonding a preferred choice for industries requiring robust and reliable product assembly.
Environmental sustainability through plasma bonding
When environmental consciousness is integral to a company’s reputation and operational responsibility, surface treatment with plasma presents a “greener” solution. Unlike conventional methods that often rely on solvents or other chemicals, plasma bonding is an environmentally friendly process. It uses ionized gas to prepare and treat surfaces, eliminating the need for substances that might harm the environment or pose health risks. Industries looking to reduce their ecological footprint find a solution in plasma bonding, as it ensures a clean, residue-free, and energy-efficient process.
Efficiency unmatched with plasma bonding
Time is a valuable commodity in production, and plasma bonding is a champion of efficiency. The entire process, from cleaning to activation and bonding, can be astonishingly quick. Within a matter of seconds, surfaces are transformed and made ready for bonding. This rapid turnaround not only speeds up production lines but also minimizes energy consumption, contributing to overall operational efficiency. For industries driven by fast-paced production schedules, plasma bonding offers a solution that keeps quality high without compromising on time.

FAQs
What is plasma bonding and how does it work?
Plasma bonding modifies a material’s surface to improve bonding with adhesives or coatings. It generates plasma by applying an electric field to a gas like argon, nitrogen, or oxygen, which cleans the surface and introduces functional groups that increase surface energy, enhancing adhesion.
Why is plasma bonding important in industries dealing with difficult-to-bond materials?
Many industries use materials that resist bonding due to low surface energy, like certain plastics and polymers. Plasma bonding modifies the surface to increase surface energy and add reactive groups, allowing stronger chemical bonds. This enables reliable adhesion where traditional methods fail.
How does plasma cleaning improve the bonding process?
Plasma cleaning uses high-energy ions and electrons to remove contaminants like oils, residues, dust, and debris from the surface. This ensures a clean surface for achieving a strong and durable bond with adhesives or coatings.
What types of gases are used in plasma bonding?
Common gases used in plasma bonding include:
- Argon: An inert gas for physical cleaning without introducing new chemical groups, effectively removing contaminants.
- Nitrogen: Adds nitrogen-containing functional groups, enhancing adhesion for certain polymers and adhesives.
- Oxygen: Adds oxygen-containing groups like hydroxyl and carbonyl, significantly increasing surface energy and reactivity.
These gases generate reactive species in the plasma to achieve the desired cleaning and activation effects.
How does plasma activation increase a material’s surface energy?
Plasma activation increases surface energy by introducing reactive groups through interaction with active plasma species. These groups, like hydroxyl and amine, raise surface energy, enhancing compatibility with adhesives and coatings for stronger bonding.
What are the main applications of plasma bonding in the medical device industry?
In the medical device industry, plasma bonding is used to:
- Ensure secure component assembly by enhancing adhesion between materials.
- Improve biocompatibility for better interaction with biological tissues.
- Enhance sterilization by removing microscopic contaminants.
- Enable miniaturization with precise bonding without added bulk.
Overall, plasma bonding improves the safety, reliability, and effectiveness of medical devices.
How does plasma bonding benefit electronics manufacturing?
Plasma bonding benefits electronics manufacturing by:
- Improvingthe adhesion of delicate components is critical as devices become smaller.
- Cleaning surfaces without damaging sensitive parts.
- Enhancing electrical conductivity or insulation through surface modification.
- Increasing reliability by forming strong bonds that resist stresses.
These benefits lead to higher-quality products and technological advancements.
In what ways does plasma bonding enhance automotive manufacturing processes?
Plasma bonding enhances automotive manufacturing by:
- Increasing durability with strong bonds that withstand extreme conditions.
- Facilitating material integration between dissimilar materials, enabling innovative designs.
- Improving component performance, enhancing vehicle safety and reliability.
- Streamlining production by accelerating assembly lines without compromising quality.
These enhancements contribute to more reliable, efficient, and feature-rich vehicles.
What are the environmental advantages of using plasma bonding over traditional bonding methods?
Plasma bonding offers environmental advantages such as:
- Eliminating hazardous chemicals, reduces harm to the environment and health.
- Energy efficiency, using less energy compared to traditional methods.
- Waste reduction, generating minimal waste without byproducts like solvent emissions.
- A clean process with no surface residue, reducing chemical cleaning steps.
These benefits promote sustainable manufacturing practices.
How does plasma bonding contribute to efficiency in production processes?
Plasma bonding enhances production efficiency by:
- Rapidly cleaning and activating surfaces, speeding up production cycles.
- Forming reliable bonds, reducing product failures and rework.
- Being automation-friendly, integrating into automated lines for consistent treatment.
- Treating a wide range of materials, simplifying inventory and supply chain management.
These factors lead to faster production, cost savings, and higher throughput without compromising quality.
Is plasma bonding compatible with cleanroom environments?
Yes, plasma bonding equipment is compatible with cleanroom standards, which is crucial for industries like semiconductor and biomedical manufacturing where contamination control is essential.
How does plasma bonding affect the long-term properties of materials?
Plasma bonding can enhance the long-term adhesion and durability of bonded materials. However, improper management can lead to changes in surface properties that may affect material performance over time, such as increased susceptibility to environmental degradation.

Video: Tantec RotoTEC-X | Corona Treatment System

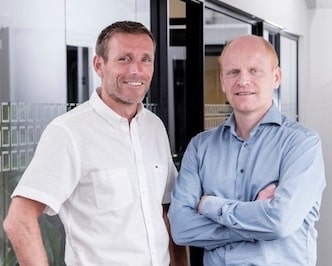
Solving your adhesion problems
We have more than 50 years of experience in delivering and manufacturing quality, high-end surface treatment products for any industry.
Tantec has both standard machines, but also custom-designed machines.
Contact us today and get a quote. We are standing by to service you.
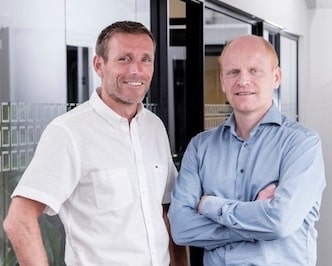
Solving your adhesion problems
We have more than 50 years of experience in delivering and manufacturing quality, high-end surface treatment products for any industry.
Tantec has both standard machines, but also custom-designed machines.
Contact us today and get a quote. We are standing by to service you.
Solving your adhesion problems
We have more than 50 years of experience in delivering and manufacturing quality, high-end surface treatment products for any industry.
Tantec has both standard machines, but also custom-designed machines.
Contact us today and get a quote. We are standing by to service you.
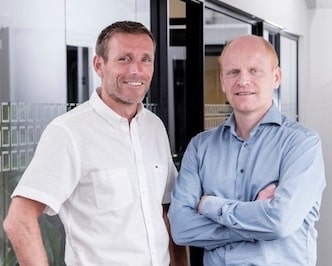
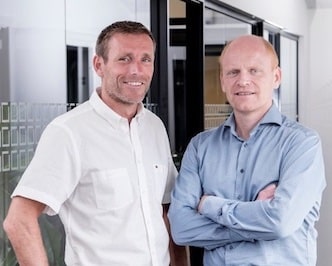
Solving your adhesion problems
We have more than 50 years of experience in delivering and manufacturing quality, high-end surface treatment products for any industry.
Tantec has both standard machines, but also custom-designed machines.
Contact us today and get a quote. We are standing by to service you.
