Tantec’s innovative ozone surface treatment helps create outstanding outdoor gear
If you have ever seen an American barbecue (in real life or in film), you may have noticed their rugged coolers with the foamy insides that keep beer and soda cold.
Well, chances are – especially if it was a high-quality cooler – that the cooler you have seen was made using Tantec’s market-leading OzoneTec solution by a leading manufacturer.
At Tantec, we have developed our OzoneTEC system to treat the interior cavity of one-piece, roto-molded products made from polyethylene so that the foam will fill the inside and adhere to the plastic shell. Examples of products include surfboards, smaller boats, toys, and outdoor coolers like the ones produced by the leading manufacturer.
Specifically, our ozone technology has helped this leading manufacturer improve their coolers to withstand both heavy use and the harshest weather conditions. Their coolers are built to become heirlooms. The following is an interview where the technical leader of the leading manufacturer explains how Tantec’s methods have helped create and improve their outstanding product.
The production setup
A cooler from this leading manufacturer is not a cheap product; however, it is a great value. The technical leader explains how they maintain reasonable prices without compromising on quality:
“We didn’t compromise on quality at all. But just by getting some modest economies of scale, we have plenty of room to grow while still holding a price point that makes the coolers accessible to more people.”
One of the reasons for the quality of their product is their production technique. Their rotational molding techniques make it possible for their cooler bodies and lids to each be molded in one seamless piece:
“What happens is the plastic comes in as a ground resin – virgin resin. It’s a medium-density polyethylene and looks like fine sand. That is poured into the molds and the molds are then bolted shut.”
“They rotate through an oven at about 550 degrees Fahrenheit for 15 minutes. The plastic liquefies and runs to each side of the mold, creating a void in the middle. That is the advantage of the roto-molding techniques, that it is all one piece – unlike with injection molded coolers, there is no glued seam or weak point where the pieces could split apart.”
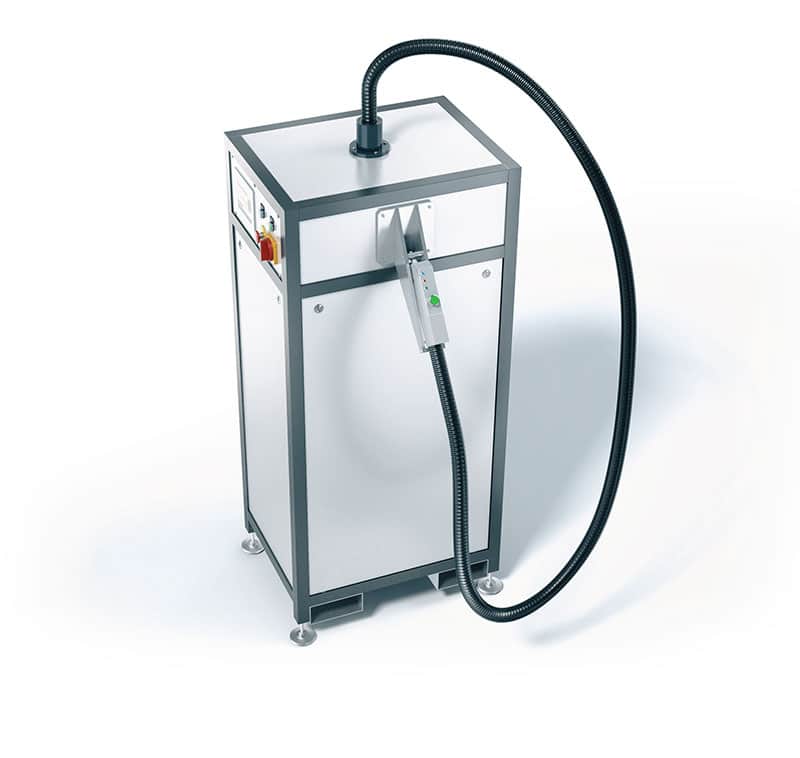
Perfecting adhesion
The technical leader explains that the void needs to be filled with foam. However, this is not a simple process, as the surface of the cooler is too slick for the foam to stick to. To allow the foam to stick, the manufacturer uses Tantec’s ozone technology to oxidize the inner surface of the plastic shell. The oxidation process preps the surface and makes it rougher. It takes the sheen off the inside surface and gives the foam something to adhere to. “The oxidation process developed by Tantec is vital for us. By infusing the cavity with the ozone with generator pumps, the plastic becomes rough enough.
The next step is that we take the coolers and lids and put them in foaming molds and inject the foam. Because of the ozone prepping, the foam glues to the walls inside.” According to the technical leader, the ozone treatment ensures that their coolers avoid delamination, which makes the plastic pop up and creates an uneven and springy surface that compromises the quality. The ozone treatment prevents that, and reveals that it is the secret to the quality of their coolers.
The best etching solution on the market
The manufacturer is always trying to improve their products and has tested other methods to roughen the insides of their coolers. However, Tantec’s OzoneTEC system is the best etching solution on the market, according to the technical leader. “I know that some try and pretreat their resin, however, we found Tantec’s solution to be the most effective way to do it. You can only access the space with a gas. Otherwise, we would have to cut the cooler shell in half and glue it back together, which would ruin the whole roto-molding concept and degrade the quality of the product.” “And their customer support is world-class. We have excellent support for everything from technical questions to access to spare parts.”
They have tried several other methods but have not found anything that compares to the ozone treatment. “We’ve not found a good alternative. We used to use packets of ozone rather than a generating machine, but the distribution was uneven. We’ve also tried to treat the resin beforehand, but this resulted in an uneven melting process,” the technical leader explains and continues: “If the plastic doesn’t melt evenly, it is more prone to deformation because the foam will come out under pressure, and if the walls are too thin in some places, it’s going to create a defective cooler.” It took the manufacturer some time to figure out their preferred method, but we are happy our OzoneTEC system could ultimately help create the greatest cooler on the market.
About the leading manufacturer
The leading manufacturer sells outdoor equipment and gear, and they take pride in making products of the highest quality that are built for the wild. The technical leader explains: “Our products are ‘gear you can trust.’ Our main product is the hard cooler, which has undergone continuous improvements to withstand the grueling environment of outdoor living. We built our cooler on the promise that it will last for generations. Our cooler is an investment in a product lasting several lifetimes.”