What is the difference between Reactive ion etching & Plasma etching
RIE is an etching method, known for its precision, control, and ability to create complex micro- and nano-structures essential in today’s electronic devices. Read on and gain insights into how reactive ion etching supports the foundational needs of industries. We will go into the nuanced operational parameters that technicians manipulate to achieve the desired etch profiles, exploring the science that makes it possible to etch thousands of layers with nanometer-level accuracy.
This article will elucidate the distinctions between reactive ion etching and plasma etching.
While both processes involve the use of plasma to remove material from a substrate, they differ significantly in their approach and the results they yield. Understanding these differences is crucial for professionals in the field to make informed decisions about the appropriate etching technology for their specific applications.
Definition and core principles of reactive ion etching
Reactive ion etching (RIE) is a key method for making tiny structures in electronic devices. It’s used a lot in making computer chips and other small tech parts. Let’s look at what RIE is and how it works.
What is reactive ion etching?
RIE is a way to etch very small patterns on surfaces. It uses gases that turn into plasma to remove material carefully. This plasma is a mix of charged particles and reactive bits.
RIE is different from wet etching, which uses liquid chemicals. Instead, RIE uses dry gases. This makes it better for creating really small and precise patterns.
How reactive ion etching works
Making plasma
RIE starts by making plasma. To do this, we put gas in a special chamber. Then we use radio waves to give the gas energy. This turns the gas into plasma.
Chemical and physical etching
RIE removes material in two ways.
- The reactive parts of the plasma react with the surface. This is the chemical part.
- Charged particles hit the surface hard. This knocks off tiny bits of material. It’s like tiny sandblasting.
Using both these methods lets RIE etch straight down with sharp edges.
Controlled direction
RIE can etch straight down without going sideways much. This helps make clear, sharp patterns.
Changing the process
We can change things to control how RIE works:
- What kind of gas we use
- How much pressure is in the chamber
- How much power do we use
- The temperature
Changing these things lets us control how fast we etch and how the final shape looks.
Using masks
We use something called a mask to protect parts of the surface we don’t want to etch. The mask is like a stencil. It lets us create specific shapes and patterns.
Why RIE is important
RIE helps us make very small and complex parts for electronics. As our devices get smaller and more advanced, RIE becomes even more important. Understanding how RIE works helps scientists and engineers make better and smaller electronic devices.
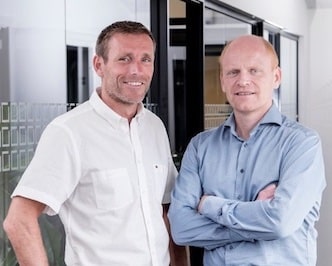
Solving your adhesion problems
We have more than 50 years of experience in delivering and manufacturing quality, high-end surface treatment products for any industry.
Tantec has both standard machines, but also custom-designed machines.
Contact us today and get a quote. We are standing by to service you.
Applications of reactive ion etching
Reactive Ion Etching (RIE) serves as a technological cornerstone in various high-tech industries due to its ability to create intricate patterns on substrates with remarkable precision. Its applications span several critical fields:
- Semiconductor manufacturing: RIE is integral in etching silicon wafers for computer chips, creating the tiny, complex structures of transistors, and other semiconductor devices. It’s used in forming gate structures, contact holes, isolation trenches, and more.
- Micro-electro-mechanical systems (MEMS): The production of MEMS devices, which combine mechanical and electrical components, relies on RIE for etching precise microstructures. These devices are found in automotive sensors, smartphones, and medical devices.
- Nanotechnology: In nanofabrication, RIE is used to etch nanoscale features for various applications, including biomedical devices, quantum computing chips, and advanced materials development.
- Photonics and optoelectronics: RIE helps in structuring waveguides, gratings, and other components necessary for manipulating light in photonic integrated circuits and optoelectronic devices.
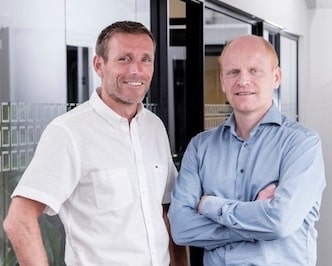
Solving your adhesion problems
We have more than 50 years of experience in delivering and manufacturing quality, high-end surface treatment products for any industry.
Tantec has both standard machines, but also custom-designed machines.
Contact us today and get a quote. We are standing by to service you.
Solving your adhesion problems
We have more than 50 years of experience in delivering and manufacturing quality, high-end surface treatment products for any industry.
Tantec has both standard machines, but also custom-designed machines.
Contact us today and get a quote. We are standing by to service you.
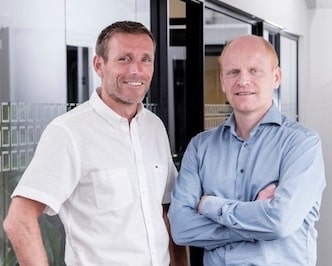
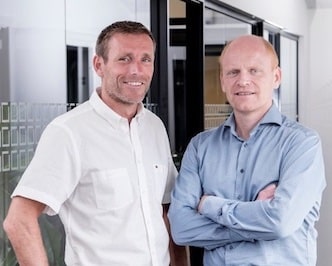
Solving your adhesion problems
We have more than 50 years of experience in delivering and manufacturing quality, high-end surface treatment products for any industry.
Tantec has both standard machines, but also custom-designed machines.
Contact us today and get a quote. We are standing by to service you.
Advantages and disadvantages of reactive ion etching
Benefits
- Precision and control: RIE offers unmatched control over feature dimensions and shapes, critical in miniaturized circuits.
- Anisotropy: The etching directionality ensures vertical sidewalls and high aspect ratio features, essential for multi-layered structures in devices.
- Material versatility: RIE can etch a wide range of materials, including silicon, metals, polymers, and more, by simply changing the gas chemistry.
- Clean process: Being a dry process, RIE reduces the possibility of contamination compared to wet etching, ensuring higher device reliability.
Limitations
- Equipment cost: RIE systems are expensive, requiring significant capital investment and operational costs.
- Maintenance: The systems demand regular maintenance for vacuum integrity, consistent plasma generation, and prevention of chamber contamination.
- Process complexity: Achieving the desired etch characteristics requires skilled technicians to fine-tune multiple parameters, necessitating a deep understanding of plasma-material interactions.
- Surface damage: The energetic ions can cause damage to the substrate surface, potentially affecting device performance.
The anisotropic nature of reactive ion etching
Explanation of etching directionality
RIE’s anisotropy refers to its ability to etch vertically down into the substrate with minimal lateral etching. This characteristic is due to the vertical trajectory of ions driven by the electric field in the plasma, ensuring that the etching primarily occurs at the bottom of the exposed features on the substrate.
Importance in micro and nanoscale fabrication
Anisotropic etching is crucial for maintaining feature integrity in densely packed micro and nanoscale devices. It allows for the stacking of multiple layers without the risk of collapsing or merging features, essential for the functionality of advanced semiconductor devices and MEMS.
Comparative techniques and technologies
Plasma etching vs. reactive ion etching
While both plasma etching and RIE utilize ionized gases to remove material from substrates, RIE incorporates both chemical and physical sputtering, facilitated by the presence of an electric field. This field aligns the ions for vertical incidence on the substrate, offering higher precision and anisotropy compared to general plasma etching, where ion bombardment is more random and less controlled.
Inductively coupled plasma (ICP) RIE
- Definition and advantages: ICP-RIE is an advanced form of RIE that uses an inductive coil to generate plasma, providing higher ion density and lower operating pressures. This results in faster etch rates, greater control over ion energy, and reduced substrate damage.
- Comparison with conventional RIE: Compared to conventional RIE, ICP-RIE offers improved control over etching processes, enabling more uniform etching for complex and high-aspect-ratio structures. It’s especially beneficial for materials requiring specific etch profiles, as it minimizes the undesired undercutting associated with standard RIE.
Reactive ion beam etching (RIBE)
- Process and uniqueness: RIBE involves the use of an ion beam in the presence of reactive gases. Unlike RIE, where plasma is generated within the reaction chamber, RIBE directs a focused ion beam onto the substrate, allowing for highly directional etching.
- Applications: RIBE is particularly suited for etching very thin films or creating small features where minimal damage and maximum depth control are crucial. It’s used in microelectromechanical systems (MEMS), nanotechnology, and specific semiconductor applications.
Surface modification and functionalization
Role in enhancing device properties
Surface modification through RIE can alter electrical, chemical, or physical properties, improving adhesion, wettability, or biocompatibility in subsequent processing steps or final device applications.
Techniques and considerations
Techniques include substrate biasing, gas pulsing, and endpoint detection. Considerations involve balancing modifications with underlying material integrity and device performance requirements.
Technical aspects of reactive ion etching
Commonly used reactive gases and their roles
Gases like SF6, CF4, and CHF3 are often used for silicon etching, while Cl2 and BCl3 are used for metal etching. The choice of gas influences the etch rate, profile, and the level of potential substrate damage.
Gas delivery systems in RIE setups
The gas delivery system controls the flow and mixture of reactive gases, impacting the etching characteristics. It typically includes mass flow controllers, mixing chambers, and valves to regulate and maintain consistent gas flows.
Power supply and electrodes: Functions and types
The power supply and electrodes generate the RF field necessary for plasma creation. The configuration (parallel-plate, triode, etc.) affects the plasma density and uniformity, influencing the etching process’s control and results.
RIE in nanotechnology and nanofabrication
Importance in the realm of nanotechnology
RIE is crucial for creating nanoscale features with high precision, enabling advancements in fields like medicine, electronics, and materials science.
Examples of nanofabrication techniques using RIE
Techniques include nanopatterning for advanced sensors, nanowire fabrication for electronics, and nanostructure creation for enhanced materials (e.g., photonic crystals).
Current state and future perspectives in RIE technology
RIE remains an indispensable tool in microfabrication, with ongoing innovations addressing challenges in uniformity, environmental impact, and new material compatibility. Its adaptability will continue to facilitate breakthroughs in electronics, healthcare, and beyond.