Plasma and Corona Treatment in the Medical Industry
In the medical industry, adhesion and coating is definitely a challenge on low surface-energy materials like polystyrene, polypropylene, polyethylene. It is important to improve the adhesion and the coating capabilities of these plastics to ensure that you can meet your FDA regulations for ink scratching, coating, and those that are important to ensure that the integrity of your medical device meets the standards required by the medical industry.
Plasma and corona surface treatment are going to modify the chemical structures on the top layer of the molecules of the plastic part. This helps ensure that you get good, uniform treatment to allow your glue, your coating, to actually attach itself to the plastic itself and ensure that you can pass your pull test or your scratch test.
Typically, we find that with plastics that have a low surface-energy, that molecules are very tightly bonded together. After a chemical or a plasma or corona treatment, we will go ahead and break these molecules apart, creating the chemical change to the surface, improving that coating or adhesion creating these peaks and valleys that will allow the surface to accept the ink or coating in a much more receptive manner.
The improved, uniform treatment ensures that you do get good cell-growth cultures, you get good wetting out of your coating, you do not have any bare or blank spots that will result in a medical product defect, resulting in recalls and not being able to meet the requirements put in place by the FDA for your product.
The article continues below the video “How do we solve these adhesion problems?”.
How do we solve these adhesion problems?
With plasma and corona treatment, they both provide a great deal of value in an environmentally friendly way replacing primers that have a lot of BOCs, that are constantly being outlawed or put more restrictions on from state to state, based on the chemical BOCs that are given off during the use of these primers.
It is not something your operators want to be exposed to on a regular basis. Environmentally friendly means that we are creating this with electricity or air and not putting any additional chemicals in front of your operators to use. These are built into machines and systems that do not require a lot of operator interface.
One of the great things about plasma and corona surface treatment is that we can do a complete treatment of the entire part, meaning that if you need the entire surface, 360 degrees to be treated, we can do that with all of our technologies. We can also shift to more of a focused or spot treatment if you will, for maybe just a specific glue area or a small area that you are trying to print on, and not treat the
whole part.
What is different about the Tantec system?
What is great about the Tantec systems is that they are unique and specialized and make the system fit your production needs instead of requiring you to change your production process in order to implement a solution like this. In many cases, you are going to find that a Tantec solution might be more than one.
There could be the use of atmosphere plasma and corona, or it could be the use of vacuum plasma or corona. We always have that ability to provide multiple solutions and technologies to achieve the nice, uniform treatment across a surface. One of the other areas that Tantec really specializes in is treating hard to reach areas on the
part: Insides of needle hubs, the inside of a syringe or a tube – all these areas that cannot be done with a standard or basic corona or plasma system.
Tantec has the ability to develop unique and interesting ways to get down inside of a part – whether it is a narrow opening, where we are trying to glue something to it, or maybe trying to ignite the inside of an entire tube without affecting the outside of the tube.
How will it affect the parts treated?
Typically, a plasma or corona surface treatment system has no ill effect on the cosmetic or structural integrity of the part.
The same part that you are producing, after a corona or plasma treatment, will still be the same part. We are not changing the overall structural integrity or the overall look or feel of the part. You cannot tell that anything has been done by the naked eye. You need some sort of method in order to measure that.
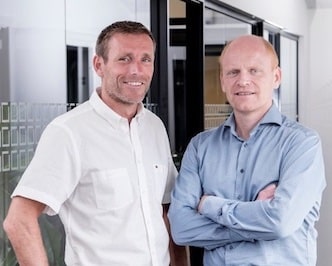
Solving your adhesion problems
We have more than 50 years of experience in delivering and manufacturing quality, high-end surface treatment products for any industry.
Tantec has both standard machines, but also custom-designed machines.
Contact us today and get a quote. We are standing by to service you.
Typical parts in the medical device industry
Needle hubs
So, some of the typical parts that we run across in the medical device industry, that are looking for some sort of corona or plasma surface treatment, are needle hubs. Simply gluing the cannula into the opening of a needle hub is a very, very challenging process without improving the wettability and the adhesion properties of a polypropylene hub.
What we typically do is, we will shoot a high voltage electrode into the opening or even use an atmospheric plasma into the opening of a hub to create wettability and adhesion improvement, so that, when the cannula is inserted and the glue is put in place, it gets good wetting and good adhesion improvement.
Another area is the syringe itself – we are looking to print on the outside of the syringe. As you might imagine, one of the big, key factors there is ensuring that the print lasts on the syringe for the life of the syringe. The last thing that anyone wants to have happened is those graduations to be scratched off or removed during transport or when a doctor is working with it.
You might imagine that the importance of giving the right dose of medicine is critical here, and that is why the print quality on the outside of the syringe is very important.
We had other requests to do the inside of the syringe as well, for whatever coating process that might be done there. It can be done in a multitude of ways, with a simple high voltage electrode being plunged into the syringe to create that functional change, as well as maybe even pumping the syringe with a gas and igniting that from
the outside, or even placing them in a vacuum chamber and allowing the plasma to working its way into the syringe, creating a nice, uniform treatment.
Catheter tubing
Catheter tubing is another area where we have got multiple uses for corona and plasma. One of the big ones is obviously printing on the catheter, putting certain bands or color markings or length definitions on there, so the doctor knows how far into the body the catheter has gone.
We want to make sure that the print does not come off the surface, so there is no risk or concern to the use of the device, as a doctor not knowing exactly how far in the body they have inserted it. The other area we all can probably appreciate is a coating on a catheter itself.
We want to make sure that this has a lubricious coating that adheres and wets out uniformly, so when it is entered into the body, it reduces the amount of discomfort in place with a catheter.
Ostomy bags
Ostomy bags are used for improving the Velcro attachment and also printing a date code on them, so that we can confirm when the product was manufactured. It is a very, very common application for us.
Life science parts
One of the more common is life sciences parts – petri dishes, cultural tissue products – where we are treating the inside of these products to go ahead and grow cells and bacteria.
As you might imagine, during the time of corona, this became very, very popular and it was extremely important to have petri dishes and cell growth culture materials to go ahead and develop these and help develop vaccines and also determine what type of viruses are growing and be able to study those very, very well.
The last area that we tend to focus on in the medical device industry is ophthalmic lenses. In the ophthalmic industry, we do a lot with lenses and coatings for anti-fog, anti-scratch etc. It is really important that we are able to get a nice and uniform coat across those surfaces, and typically, with a polycarbonate or something along those lines, getting those coatings to stick to the surface is a big challenge.
We want a nice, thin layer on there, as we do not want to bulk up the lens itself and cause a change in the overall properties of the plastic, which is activated and modified.
Tissue culture products
Poor adhesion on tissue culture products – multiwell plates, petri dishes, flasks etc. is important. We need to get a nice, uniform treatment across those surfaces, so that, when bacteria and things like that are grown inside there, it does not result in a failure just because the bacteria was not able to grow uniformly across the surface.
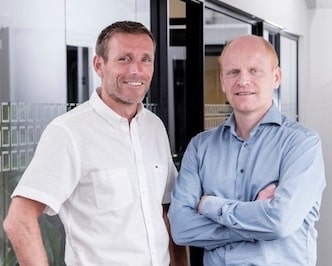
Solving your adhesion problems
We have more than 50 years of experience in delivering and manufacturing quality, high-end surface treatment products for any industry.
Tantec has both standard machines, but also custom-designed machines.
Contact us today and get a quote. We are standing by to service you.
Solving your adhesion problems
We have more than 50 years of experience in delivering and manufacturing quality, high-end surface treatment products for any industry.
Tantec has both standard machines, but also custom-designed machines.
Contact us today and get a quote. We are standing by to service you.
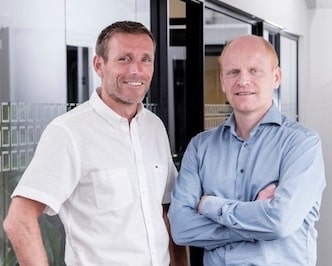
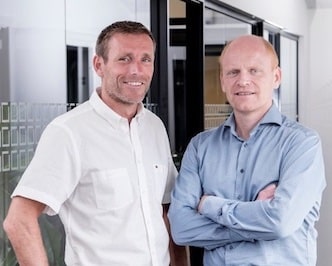
Solving your adhesion problems
We have more than 50 years of experience in delivering and manufacturing quality, high-end surface treatment products for any industry.
Tantec has both standard machines, but also custom-designed machines.
Contact us today and get a quote. We are standing by to service you.
Polypropylene is difficult to treat
Polypropylene is a very, very difficult material to treat, especially in the medical device industry, so it is very important that a plasma or corona treatment is put in place in order to ensure that the ink or those graduations on the syringe will adhere well and also print out in a good resolution, so that the doctors can see what they are doing.
For the needle hubs, it is a really unique and specialized design where Tantec has to pull the electricity from the corona right into the opening and down through the needle hub, ensuring the overall adhesion of that glue, when the cannula is inserted.
At the ostomy pouches we are trying to glue that Velcro tape down to make sure that it does not peel off very easily – so that is typically done with a corona-based system – as well as the print quality or the good adhesion of the print itself for date codes and product information to ensure that if there is a problem with the product or anything along those lines, there is traceability and trackability on these particular products.
Lenses
Ophthalmic lenses are typically a polycarbonate-based material. Lens coatings are a major value add to the glass industry – or the glasses industry. Anti-fog, anti-scratch, transitions coloring etc. all those things that people look for on their glasses to improve the quality and overall use of their glasses is important.
When you start building those layers of coatings over and over again, you want to make sure that each layer adheres properly. We do not want to have these build-ups of coating, so we have to put additional material on, because it is not wetting out well.
We also do not want to have cases where the coating flakes off or scratches off too easily. As well as you do not want little defects like fish eyes or small pockets that did not coat, resulting in a poor quality lens, and the customer will ultimately reject and need to have the lens remade at that point.
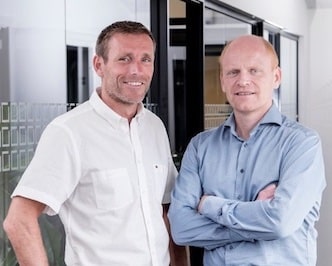
Solving your adhesion problems
We have more than 50 years of experience in delivering and manufacturing quality, high-end surface treatment products for any industry.
Tantec has both standard machines, but also custom-designed machines.
Contact us today and get a quote. We are standing by to service you.
Tantec experience
Tantec has been working in this industry for more than 20 years. We have a variety of different solutions here with corona or plasma as possible technologies that can improve your process.
Accepted technology in the medical device industry
When it comes to getting a product FDA-approved, they have to pass several levels of testing. When the product makes it to the market, there is no risk to the patient. Tantec has a lot of experience in the medical device industry and helping customers achieve FDA approval by adding a plasma or corona process.
Plasma and corona is an accepted technology in the medical device industry. It is used in a lot of FDA-approved products, so there is no concern that you are introducing a new technology to an industry that requires additional testing or regulation.
Tantec-systems that are used in the medical device industry
RotoTEC
One of the big ones is our RotoTEC, which is a rotational, corona-based process.
This has rotating dishes and electrodes that are creating a high-voltage field, as a part passes underneath that. This product is very unique and specialized and that rotation provides a very nice and uniform treatment. It also allows for the treatment of larger parts that are taller, creating a good, uniform treatment across a large part
or also down into the base of a part that might have taller sidewalls.
It is used quite often for tissue culture products like petri dishes, multiwell plates, flasks, also used for ophthalmic lenses and just about any other type of shaped part that needs treatment around the sides of the part or down inside an open cavity of the part itself.
SyrinTEC
Another area that we have a lot of experience with is our SyrinTEC, which is our syringe treatment system. It allows for the parts to be hanging and passing through a corona field – almost like a curtain of corona that will then treat the entire syringe, 360 degrees.
Not only do we treat the outside of the syringe, but we can also treat the inside of the syringe, or even the inside of a tube, or a cuvette, or something along those lines, where you need interior wall treatment to get your media to go ahead and wet out and spread out onto the interior of the surface.
Needle hubs
Needle hubs are an area where we have multiple technologies. We have two different types of coronas that can work with needle hubs, as well as atmospheric plasma, giving you a nice opportunity to integrate a system without affecting too much of your current process.
With needle hubs, we can run systems with up to 18.000 parts per minute, which means that we can do a really, really high speed. We can also develop systems for low speed.
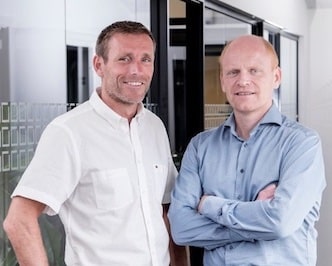
Solving your adhesion problems
We have more than 50 years of experience in delivering and manufacturing quality, high-end surface treatment products for any industry.
Tantec has both standard machines, but also custom-designed machines.
Contact us today and get a quote. We are standing by to service you.
Contact us with an unique challenge
Keep in mind that these are only some of our technologies. If you have a unique challenge with your medical device product, that is certainly something Tantec is open to discuss with you and investigate a little bit further, providing you with some possible solutions.
Free sample testing
One of the areas that we like to notify our customers of is that we have a full lab in our office in Chicago as well as our home office in Denmark, where we do free sample testing to help evaluate your material, your process, help prove out what we can do in terms of providing that improvement in surface energy, which should then
result in better adhesion, better coating, better print quality.
Test the parts and its value
No matter what we do in terms of surface energy change, it is important to put the part through your final test process. Changing surface energy does not always equate to better adhesion or better coating.
We are able to treat the part, we are able to provide you an improvement in surface energy, but at the end of the day we need you to go ahead and test the part and confirm that it does provide that value add, you are looking for!