What is Plasma Cleaning Used For?
This article has been reviewed and verified by Jeff Gradus, VP & Surface Treatment Expert Specializing in Corona and Plasma Technologies.
This article has been reviewed and verified by Jeff Gradus, VP & Surface Treatment Expert Specializing in Corona and Plasma Technologies.
This article has been reviewed and verified by Jeff Gradus, VP & Surface Treatment Expert Specializing in Corona and Plasma Technologies.
Why use Plasma Cleaning equipment?
Cleaning is required for the removal of contaminants from surfaces before they can be used in the manufacturing process. This cleaning can be achieved by using plasma cleaning equipment or plasma cleaning machines.
Plasma cleaning can be applied to an array of materials along with surfaces with complex geometries.
A plasma cleaning system allows the efficient cleaning of a surface without having a negative impact on other properties of the surface.
Over the past few decades, the efficiency of plasma cleaning has been recognized, and used for a variety of pre-processing cleaning of materials.
The following video provides some information on what plasma cleaning really is and what it’s used for.
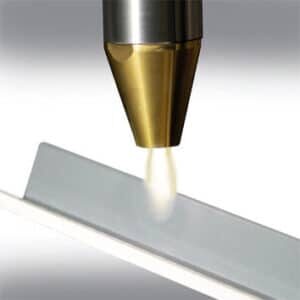
What is Plasma?
Plasma is considered as the fourth state of matter. It is a unique processing medium when it comes to treating surfaces and for surface modifications. Plasma is ionized gas that consists of ions, electrons and neutral atoms.
While electrons in the plasma exist at a higher temperature as compared to neutral gas, the plasma is always at near-ambient temperature with the density of its electron being around 1010 cm-3.
Plasma cleaning has the capabilities to effectively remove all organic contaminations from surfaces through the process of a chemical reaction (air plasma) or physical ablation (Ar plasma/ Argon plasma).
A plasma cleaning system also works with chemical functional groups, such as, carboxyl, carbonyl and hydroxyl on the surface, which results in rendering most surfaces hydrophilic. Apart from being clean, a surface also has got to be hydrophilic, i.e. having a decreased amount of water contact angle with an increase in wettability in order to enhance the bonding or adhesion to other surfaces during the manufacturing process.
Apart from that, plasma cleaning is also used to remove microbial contaminants from a surface, which makes it extremely beneficial for sterilization in biomaterials research applications.
Wanna know more? Read about plasma treatment.
How does plasma cleaning compare to traditional cleaning methods?
Plasma cleaning offers several advantages over traditional cleaning methods:
- Effectiveness: Plasma cleaning is more effective at removing contaminants, including organic and microbial contaminants, from surfaces. It can clean deeply into microscopic peaks and troughs, ensuring a thorough clean.
- Environmental friendliness: Unlike traditional wet chemical cleaning, plasma cleaning is environmentally friendly. It eliminates the need for chemical solvents, reducing the environmental impact and the need for solvent storage and disposal.
- Safety: Plasma cleaning is safer for operators as it does not involve handling hazardous chemicals.
- Cost efficiency: The operational costs of plasma cleaning systems are low, and the annual maintenance costs are negligible. This makes it a cost-effective solution compared to traditional methods.
- Surface integrity: Plasma cleaning does not negatively impact the properties of the surface being cleaned, unlike some traditional methods that can be harsh and damaging.
- Ease of use: Plasma cleaning systems are operator-friendly and easy to use, making them a convenient option for various industries.
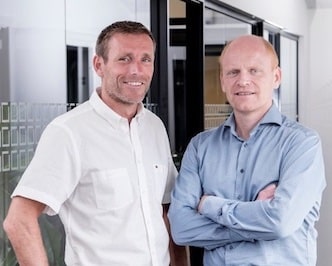
Solving your adhesion problems
We have more than 50 years of experience in delivering and manufacturing quality, high-end surface treatment products for any industry.
Tantec has both standard machines, but also custom-designed machines.
Contact us today and get a quote. We are standing by to service you.
Plasma Cleaning Applications
Plasma cleaning systems can be used for a variety of surface cleaning purposes before processing. It is efficient for removing surface oxidation and clearing mineral residue from surfaces.
It is also used for preparing surfaces of plastics and elastomers, as well as for cleaning ceramics. It is also used for cleaning the surface of glass, as well as metal surfaces.
Using efficient plasma cleaning systems eliminates the need for using chemical solvents.One major benefit of using plasma cleaning is that the entire process is operator friendly and environmentally friendly.
Apart from that, the operational cost of using plasma cleaning systems are low, while providing the highest quality in cleaning surfaces. Another benefit of using a plasma cleaning system is that it eliminates the need to use chemical solvents.
As a result, using plasma cleaning eliminates the need for storage facilities or for making arrangements for solvent waste disposal. Plasma is a proven and effective method for critical surface preparation.
What role does plasma cleaning play in surface preparation for bonding?
Plasma cleaning plays a crucial role in surface preparation for bonding by:
- Removing contaminants: Plasma cleaning effectively removes organic contaminants from surfaces, including those in microscopic peaks and troughs, ensuring a clean surface for better adhesion.
- Surface activation: The process activates the surface of materials, increasing their surface energy. This improved surface energy enhances wettability and adhesive properties, making it easier for coatings, inks, and adhesives to bond.
- Consistent and reliable results: Plasma cleaning provides consistent and reliable cleaning, ensuring that surfaces are uniformly prepared for subsequent manufacturing processes.
- Environmentally friendly: It is a cost-effective and environmentally friendly process, eliminating the need for chemical solvents and reducing waste.
These benefits make plasma cleaning an ideal solution for improving adhesion in various manufacturing processes, including bonding, painting, varnishing, and coating.
What is Oxygen Plasma Cleaning?
Oxygen plasma refers to any plasma cleaning process where oxygen is also used in the plasma chamber. Oxygen is also used in cleaning processes that are carried out before bonding. Oxygen can also be combined with other gasses as well to etch a surface.
It wouldn’t be wrong to say that oxygen is the most common gas that is used in plasma cleaning. This is mainly due to its wide availability and low cost. Oxygen plasma can be created by using an oxygen source in a plasma system.
Furthermore, all systems available for plasma etching can work with oxygen, since it is commonly used to clean non-metal surfaces such as glass, Teflon, and plastics, and also increases the non-metallic surface’s wettability.
What are the differences between air plasma and argon plasma cleaning?
Air plasma cleaning involves a chemical reaction that effectively removes organic contaminants, while argon plasma cleaning uses physical ablation to clean surfaces. Each type is suited to different applications depending on the specific contaminants and surface materials involved.
Plasma Cleaning Costs
The cost of plasma cleaning equipment is relatively cheap compared to other material surface cleaning systems. Apart from that, the costs that go into the equipment’s annual maintenance are also negligible, which is why the popularity of plasma cleaning has grown significantly over the years.
Plasma cleaning is considered an effective and easy-to-use method to achieve better cleaning results over conventional cleaning processes.
Plasma cleaning should be applied wherever a clean and reliable surface is needed. Plasma cleaning is not only easy and safe but also environmentally friendly, and far more effective than traditional wet chemical cleaning procedures.

Video: VacuTEC | Vacuum Plasma Treater

