The Impossible Trio, Solved: Greener, Cheaper and Stronger Adhesion Made Possible on an Industrial Scale
A new partnership between Tantec and the American company Reliabotics has paved the way for a superior industrial adhesion process. This process is not only cheaper than traditional ones, but also ensures stronger adhesion whilst being easier on the environment.
By combining Reliabotics’ sophisticated carbonic cleaning expertise with our plasma and corona technology, the new solution can deliver superior adhesive qualities without introducing stronger chemicals or more tedious processes. In fact, the joint venture enables fully automated preparation and adhesion processes without the need for human intervention.
The process ensures stronger, higher quality adhesion — something that may seem trivial if you consider only low-cost consumer products. However, if you consider the markings on an artificial hip, the measurements on a medical syringe or even the paint and coating on your car, adhesive strength suddenly becomes critical.
In this article, we will introduce you to the essential preparation process leading up the actual gluing. Preparation, as you’ll learn, is a prerequisite for any glue to work, no matter the material.
Better Cleaning Means Better Adhesive Qualities
Gluing something onto an oily surface can be difficult or even impossible. For the glue to work properly and with the highest adhesive power possible, you need to thoroughly clean the part before applying the glue.
Even if the part looks and feels clean, the micro- and nano-levels of the surface will reveal oil, grease, and dust from the factory — all of which will diminish the adhesive qualities of the part and consequently put the part’s quality at risk.
At the micro-level, any surface (no matter how smooth) consists of miniature crests and valleys that attract and capture grease and dust particles, preventing the glue from sticking to those crests and valleys.
To clean the surface thoroughly, you need to dissolve grease and oil, as well as remove dust particles from the microscopic valleys.
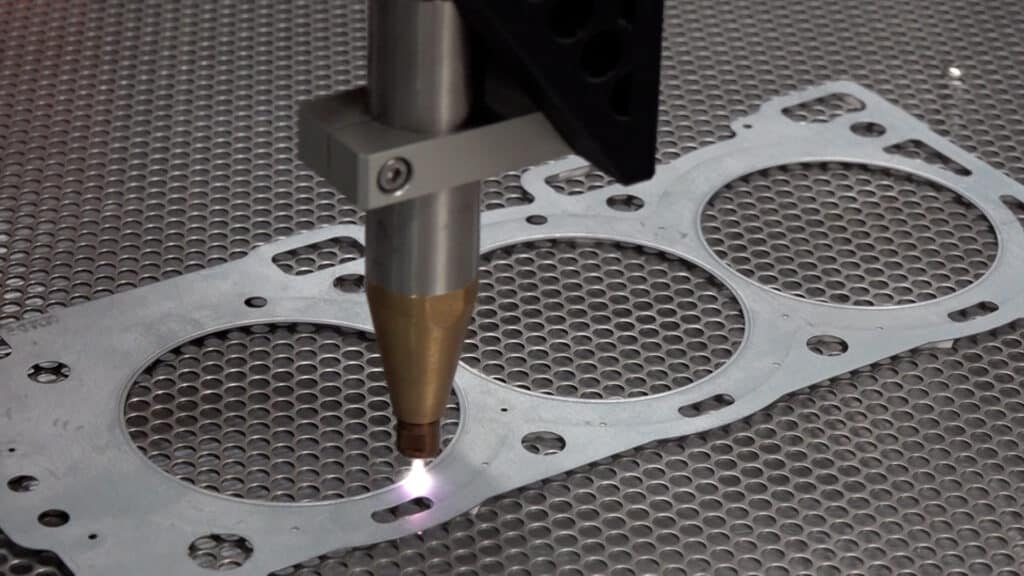
Where Traditional Cleaning Methods Fail
While alcohol wipes may dissolve some of the grease and chemical washing may remove most dust and grease, new studies have shown that carbonic cleaning (also known as dry ice cleaning) is by far a superior method of cleaning parts. Carbonic cleaning “shovels” away dust particles, dissolves grease and is able to clean even the smallest crevices in the surface.
Traditionally, dry ice cleaning has been reserved for larger and more durable parts. The technology has relied on crushing pellets of frozen carbon dioxide into particle-sized bullets and shooting them at high velocity onto the surface that needs cleaning.
However, this method requires manually loading pellets and constant human supervision. Furthermore, traditional dry ice cleaning is a harsh method, which renders it useless when cleaning materials like glass, brittle plastic or delicate electronic parts.
Solving the Dry Ice Issue
With the introduction of Reliabotics’ new method of carbonic dry ice cleaning, all of these drawbacks can be eliminated.
The need for frozen pellets is replaced by a simple supply of CO2 in liquid or gas form. For large-scale cleaning needs, a CO2 tank can be installed next to the nitrogen and oxygen tanks outside the factory building. For smaller cleaning needs, bottles of CO2 can be connected directly to the cleaning nozzle.
The simple supply of CO2 opens the door to a fully automated cleaning process, making human supervision unnecessary. As the cleaning nozzle is small enough to fit on an ordinary industrial robotic arm, the process can be preprogrammed into the robotic arm and enter a fully automized production line.
The new method even moderates the harshness of traditional dry ice cleaning without compromising the thoroughness and quality of cleaning. The cleaning nozzle processes a dry ice stream soft enough to clean glass surfaces, electronic equipment, and plastics, while it remains strong enough to clean industrial steel components with oily surfaces. This is a combination unique to this technology.
However, meticulous cleaning also comes with a cost: the carbonic cleaning process lowers the surface energy of the object to a level so low that adhesives have nothing to “hold on to.” The surface becomes “too clean,” so to speak.
For adhesives to achieve their full potential and secure strong and safe attachments, you need to reactivate the surface energy — a process we refined at Tantec for more than 40 years.
Plasma Technology Activates and Intensifies Adhesive Qualities
In essence, plasma is the fourth state of matter. While you may recall the three “ordinary” states of matter from school — solid, liquid and gas, — the fourth state is less well-known.
The fourth state, plasma, occurs when matter is heated beyond the gas state to a state where the individual atoms detach from the molecules entirely and float around freely. This happens at around 3,000 K (4,940 F). To clarify, when a substance is in the gas state, atoms are still bound to the molecule when they are floating around in the air.
In a lab or a factory, newer technologies allow plasma to be created at much lower temperatures, under a controlled process and at industrial scales.
Plasma Treatment — Superior Technology
The benefits of plasma treating are not easily overlooked.
Firstly, exposing parts to plasma treatment helps clean the surface of the part at the nano-level. While plasma cleaning is not as efficient as the carbonic cleaning mentioned above, plasma cleaning can be sufficient where cleaning does not need to be as vigorous.
Secondly, plasma treatment is the most efficient method of activating surface energy of the part. By introducing parts that have undergone a carbonic cleaning to plasma treatment, you get the best of both worlds: an industriously cleaned surface with no grease or dust to block adhesion and a fully energized surface with maximum adhesive qualities.
Lastly, plasma treatment is the only surface energy activation technology that can be introduced on an industrial scale without jeopardizing parts or the environment and without straining your bottom line.
The combination of Tantec’s plasma treatment and Reliabotics’ new form of dry ice cleaning provides full certainty that whatever you want to glue together will stick as long as possible.
A Greener and Cheaper Alternative
Today, preparation before gluing typically involves extensive washing and subsequent drying. This process is a costly affair, both for the environment and for finances.
Washing involves harsh, expensive chemicals, as well as vast amounts of water. Both the chemicals and the water consumption come with an environmental price. This is a price that consumers, governments, and companies themselves are increasingly aware of and unwilling to pay.
Consumers are already demanding “green” products with small or no environmental footprint. To compete in the future, companies must take the green agenda seriously and adjust products and production to minimize environmental impact.
In this regard, replacing traditional chemical washing with modern carbonic cleaning and plasma treatment is an important step.
Although carbonic cleaning utilizes CO2, mechanisms that capture the CO2 after cleaning have already been implement in several places. The technological solutions for a CO2-neutral dry ice cleaning process are already available.
Looking at plasma treatment, environmental impact is limited to including the energy consumption involved in the process. Consequently, buying electricity from sustainable sources is the only initiative needed to secure an environmentally friendly plasma treatment.
Financially Sustainable
Eliminating industrial washers from the factory floor provides more than one financial benefit.
Firstly, the simple act of removing the washers and replacing them with robotic arms that can operate both the carbonic cleaning nozzle and the plasma nozzle will save costly space on the factory floor. It’s a smaller unit capable of producing the same outcome or even a better one.
Secondly, both technologies fit onto standard industrial robotic arms. Therefore, the cleaning process can be employed both as a separate unit ready for fixed objects or as part of a fully automized production line.
None of these technologies require human supervision and supplying the necessary gasses requires only a few pipes connected to the outside tanks.
Thirdly, while the gasses needed for the process are not free, the costs of water and chemicals far exceed those of acquiring the necessary gasses. Depending on the previous process and the nature of the part that needs cleaning, companies save between $4-8 per hour on primer and between $10-15 per hour on water and chemicals for washing.
All in all, the new duo of carbonic cleaning and plasma treatment truly does cater to the triple bottom line, giving you a cheaper alternative with higher quality and a smaller environmental footprint.
