Vacuum Plasma Treatment Improves Adhesion Capabilities
The results of plasma treatment of surfaces are present in your everyday life, even if you aren’t aware of it.
Just look at the keyboard on your computer – chances are, it has been through plasma treatment before the symbols and numbers were added to the keys.
This is because plasma treatment ensures better adhesion, making the numbers and symbols stick to the keys better and prevent them from being rubbed off during normal daily use.
It is not only the keyboard that has been through that treatment though. Your car keys have too, any place in your kitchen that has writing, like the oven and stove settings, maybe your water bottle or pen has a logo on it. Here, plasma treatment ensures not only enhanced adhesion, but also that the logo can be transferred in a way that makes it crisp and sharp compared to the background.
It is not only relevant for those daily things that, strictly, we could live with even if the added details were rubbed off. Adhesive strength becomes a lot more important when we talk about the markings on an artificial hip or the measurements on a medical syringe.
To run a pen or a syringe through a plasma treatment machine is a fairly simple process because of their size, but things like interior panels for cars have proved a challenge in the past, because of their size and geometry. This challenge has been met by the Vacuum Plasma Treatment.
What is Vacuum Plasma Treatment?
Vacuum Plasma Treatment is, to put it simply, plasma treatment in a vacuum. But let’s begin by looking at what plasma and plasma treatment is.
Plasma is the fourth state of matter, the other three being solid, liquid and gas. This fourth state is less well-known, perhaps because it does not occur naturally on Earth as frequently as the other three states. Lightning and the northern and southern lights are examples of naturally occurring plasma, but aside from those, plasma is primarily found in space.
Plasma occurs when matter is heated beyond the gas state, causing the individual atoms to detach from the molecules entirely and instead float around without restraint. This requires a temperature of around 3,000 K (4,949 F), but newer technologies have made it possible to create plasma at much lower temperatures, during a controlled process and at an industrial scale, by using high voltage electric discharges.
Vacuum Plasma Treatment in Manufacturing
In manufacturing, plasma treatment is a way to clean the surface of the treated part at a nano-level. This has previously been limited to the specific spot where the plasma discharge hit the part, but by placing the part in a vacuum chamber, it is now possible to treat even very large parts with an even and unvarying finish.
This means that where, for example, a car panel used to be difficult to treat because the discharge would not be able to reach all the nooks and crannies, today a vacuum plasma treatment setup, solves this problem.
Looking inside the vacuum chamber, you will find an electrode at the top and one at the bottom. Once the air has been removed from the chamber, a high voltage discharge is ignited, which creates a plasma plume between the two electrodes. The plume provides a very focused amount of energy, that will encapsulate the entire part. The part can remain stationary as the vacuum ensures the plasma plume covers everything, giving the part a 360° treatment.
Why Vacuum Plasma Treatment Works So Well
As explained, plasma treatment improves the adhesion capabilities of the surface greatly. In other words, plasma treatment changes the surface energy, and improves the wettability of the surface.
Wettability is the ability of water to make contact with the surface of something. When wettability is low, the surface is hydrophobic. This means that water or similar liquids will gather in droplets, retaining as little surface contact as possible. However, if the surface has undergone plasma treatment, it will instead be hydrophilic, and the water will spread out to cover as much of the surface as possible.
This means that less liquid is needed to cover the surface. Within the previously mentioned medical equipment that also undergoes this treatment, tissue culture samples gain further benefit from the plasma treatment because the increased wettability also means improved and confluent growth of cells in them.
Will Vacuum Plasma Treatment Change the Product’s Appearance?
The short answer is no. Regardless of what properties are desired as a result of the plasma treatment, whether an improvement in the adhesion value or an increase in wettability, the plasma treatment does not cause a visible alteration in the part.
Because the treatment changes the surface at a nano level, the change will be visible under a high-power microscope, or when doing testing to test wettability via contact angle measurement or dying solution application. However, to the naked eye the part will look exactly as it did before the treatment.
In other words, plasma treatment adds value to the parts without changing the appearance of them. This means that the plasma treatment will not negatively affect the production processes that come afterwards. The positive effects of the plasma treatment will, however, be very apparent when the wettability is improved and the adhesion value is raised, providing products that can perform even better than before.
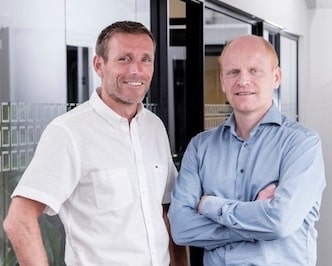
Solving your adhesion problems
We have more than 50 years of experience in delivering and manufacturing quality, high-end surface treatment products for any industry.
Tantec has both standard machines, but also custom-designed machines.
Contact us today and get a quote. We are standing by to service you.
Solving your adhesion problems
We have more than 50 years of experience in delivering and manufacturing quality, high-end surface treatment products for any industry.
Tantec has both standard machines, but also custom-designed machines.
Contact us today and get a quote. We are standing by to service you.
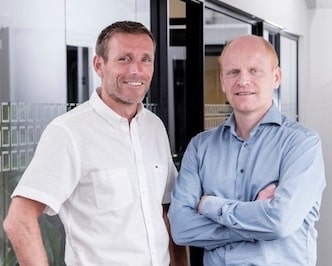
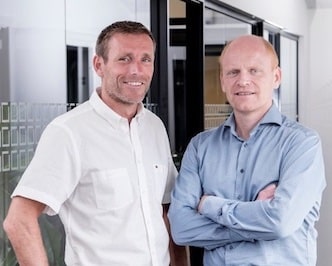
Solving your adhesion problems
We have more than 50 years of experience in delivering and manufacturing quality, high-end surface treatment products for any industry.
Tantec has both standard machines, but also custom-designed machines.
Contact us today and get a quote. We are standing by to service you.
Surface treament FAQ
Can I treat 3D objects with plasma?
A plasma treatment is the ideal solution for your 3D parts because plasma gets almost everywhere. Therefore, it can cover regions of your parts which cannot be reached by traditional treatment methods. You can even treat the inside of small parts like syringes or the inside of a closed plastic bag.
Feel free to send us a sample of your part and explain your project to us – we will then conduct a free test of your part in our in-house testing facilities and advise you in the best possible treatment solution!
Can the treatment be limited to certain parts of an object?
Theoretically, we could limit a treatment to certain regions by covering parts of an object. However, a plasma treatment usually does not have any negative side-effects for the treated object so in most cases, there would be no reason to do so.
How do I evaluate the success of a plasma treatment?
We provide different measurement techniques including surface energy test inks and pens as well as contact angle measurements to measure the effectiveness of your plasma treatment. Do not hesitate to get in touch with our experts, so we can help you find the most effective treatment for your individual demand!
Is in-line treatment possible?
Of course. We supply both standalone plasma treaters and in-line plasma treaters, which can easily be integrated into your existing production process. Do not hesitate to contact our experts to discuss how a plasma treatment can be integrated into your existing production line!
Which sizes can be treated?
We offer treatment solutions for almost any size. Smaller parts are often placed on trays, so that many parts can be treated simultaneously.